Inconel 625
Inconel 625 is a high-performance nickel-chromium-based alloy known for its possession of high strength properties as well as its high resistance to corrosion, oxidation, and high temperatures. This alloy performs remarkably well in harsh environments, such as those with extreme temperatures or exposure to aggressive chemicals. Its excellent properties make it a common choice for applications in industries like offshore, oil and gas, maritime, and chemical processing. However, while it offers great protection, modern laser cladding technologies as offered by Topclad, provide even more targeted, durable solutions for component protection.
What is Inconel 625?
Inconel 625 is an alloy primarily composed of nickel and chromium, combined with elements like molybdenum and niobium, which together give the alloy its resistance to corrosion and oxidation. This combination allows Inconel 625 to maintain its structural integrity and performance in extremely harsh conditions, including high temperatures and aggressive chemical environments. Its non-reactive nature also makes it a solid choice for high-stress applications, particularly where both corrosion and mechanical stress are present.
Inconel 625 is a nickel alloy composition and includes:
- Nickel (Ni): provides excellent resistance to oxidation and corrosion
- Chromium (Cr): enhances resistance to oxidizing chemicals
- Molybdenum (Mo) and Niobium (Nb): provide strength and resistance to non-oxidizing acids
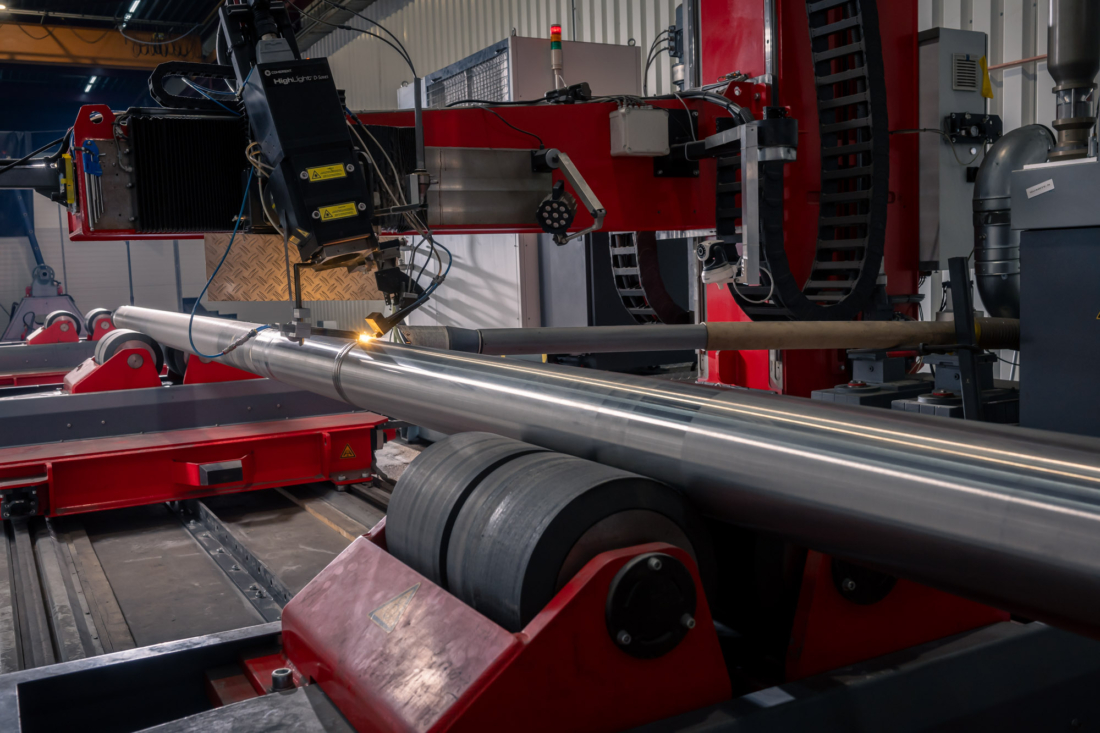
Key properties
- Outstanding corrosion resistance (saltwater, acids, oxidizing and reducing environments)
- High tensile strength and fatigue resistance
- Oxidation resistance up to ~980°C
- Excellent weldability and formability
- Non-magnetic, stable in harsh environments
Manufacturing forms: Inconel 625 is available as plate, bar, pipe, welding wire, and powder – making it versatile for various industrial uses.
Chemical composition and technical details
Typical chemical composition:
- Nickel (Ni): 58–63%
- Chromium (Cr): 20–23%
- Molybdenum (Mo): 8–10%
- Iron (Fe): up to 5%
- Niobium (Nb): 3.15–4.15%
- Carbon (C): max 0.10%
This composition gives Inconel 625 its unique combination of strength, corrosion resistance, and high-temperature stability.
Inconel 625 price per kg
The price of Inconel 625 per kilogram can vary depending on form, volume, and market conditions. As a premium alloy, it is generally priced higher than common steels or stainless steels.
- General price range: Inconel 625 typically ranges between €30 and €50 per kg, depending on supplier, form (e.g., powder vs. bar), and market conditions such as nickel price volatility.
- Factors affecting price: Order volume, form (e.g., plate, pipe, wire), heat treatment, certifications, and availability.
- Disclaimer: These prices are indicative. For accurate and current pricing, request a quote based on your specifications.
This makes laser cladding with Inconel 625 an economically attractive alternative, since far less material is required.
Inconel 625: Key Benefits & Disadvantages
While Inconel 625 offers outstanding material properties, it’s not the perfect solution for every application. Here is a balanced overview:
Benefits:
- Corrosion Resistance: Inconel 625 stands out for its ability to resist corrosion, even in environments with saltwater exposure, acids and other harsh enviroments.
- Heat resistance: It can withstand extreme temperatures, maintaining its strength and integrity at both high and low temperatures.
- Oxidation Resistance:The alloy’s resistance to oxidation makes it particularly useful for components exposed to high-temperature combustion environments, such as furnaces and exhaust applications.
- Strength & durability: Excellent fatigue and creep resistance, making it a strong material for demanding applications.
- Weldability: Performs well in fabrication and repair operations.
Disadvantages:
- High costs: Inconel 625 is considerably more expensive than many other materials due to its complex composition and the costs associated with its production.
- Machining difficulty: The toughness of Inconel 625 makes it more difficult to machine, requiring specialized tools and processes.
- Density/weight: Inconel 625 is dense (~8.4 g/cc), which means components are heavy compared to aluminum or even steel. In weight-sensitive designs (like aerospace) this can be a drawback.
What is Inconel 625 used for?
- Offshore Oil and Gas: Inconel 625 is widely used in offshore oil and gas applications for components such as pipes, valves, and pumps that are exposed to corrosive seawater and high pressures.
- Maritime Applications: Inconel 625 is extensively employed in the maritime industry for propeller shafts, fasteners, and other components that must withstand the corrosive effects of seawater. Its resistance to saltwater corrosion makes it ideal for shipbuilding, offshore platforms, and dredging utilities.
- Chemical Processing: Inconel 625 is commonly found in chemical processing plants where components are required to resist aggressive chemicals and high-temperature environments.
Inconel 625 vs 718: What’s the difference?
Both Inconel 625 and Inconel 718 are nickel-based alloys, but their compositions and applications differ. Inconel 625 contains higher amounts of molybdenum and niobium, providing superior resistance to corrosion and oxidation, making it more suitable for seawater and chemical exposure. In contrast, Inconel 718 has higher tensile strength and is often used in high-temperature applications where strength and creep resistance are critical, such as aerospace. While both alloys are highly durable, Inconel 625 is the better choice for corrosion resistance, while Inconel 718 excels in mechanical strength and heat resistance at extremely high temperatures.
Inconel 625 vs stainless steel 304 or stainless steel 316
Inconel 625 outperforms 304 and 316 stainless steel in terms of corrosion and heat resistance, especially in harsh marine or chemical environments. However, it is also more expensive (per kg) and harder to machine.
304/316 are suitable for less aggressive applications, whereas Inconel 625 is reserved for critical environments requiring maximum durability.
Alternative for solid Inconel 625
While Inconel 625 is highly effective, manufacturing entire components from it can be prohibitively expensive. This is where laser cladding (or weld overlay) provides a smart, high-performance alternative.
Why choose laser cladding over solid Inconel 625 or HVOF spraying?
While HVOF (High Velocity Oxy-Fuel) spraying and solid Inconel components are both proven solutions, laser cladding offers a smarter, more efficient approach in many industrial scenarios.
- Material efficiency and cost savings
Instead of manufacturing entire parts from Inconel 625 — which is costly and material-intensive — laser cladding applies a thin, high-performance layer exactly where it’s needed. This drastically reduces Inconel 625 usage and overall material costs. - Targeted protection, not over-engineering
Only the functional surfaces are coated, avoiding unnecessary alloy use in low-stress zones. This results in a lighter, more economical component without compromising performance. - Superior bonding and performance
Unlike HVOF, which relies on mechanical adhesion, laser cladding forms a metallurgical bond with the base material. The result: a stronger, more durable layer that performs like solid Inconel 625 — but only on the surface. The layer thickness can be tailored to match wear profiles, from sub-millimetre precision to multi-millimetre durability. - Design flexibility and long-term value
If the surface layer eventually wears down, it can be machined off and re-applied, extending the component’s life without replacing the whole part. This makes laser cladding ideal for repair, rebuild, and life extension of critical components.
Compared to both solid Inconel parts and HVOF coatings, laser cladding provides the optimal balance of performance, precision, and cost-effectiveness — especially in applications where corrosion, wear, and heat resistance are critical.
What is laser cladding?
Laser cladding uses a laser heat source to deposit a thin layer of Inconel 625 onto a base material, such as carbon steel. This creates a bimetal component with the performance of Inconel 625 where it’s needed, and the cost-efficiency of common steel elsewhere.
Why laser cladding is superior
Compared to other surface treatments, laser cladding offers:
- Low dilution and precise control
- Minimal distortion due to focused heat input, preserving the properties of both the base and the alloy.
- Higher hardness and durability
- Reduced post-processing from thin, smooth layers
Topclad offers proprietary engineered coatings (such as Quarite N) that can even outperform pure Inconel 625 in some applications.
Other products in this serie
Aluminium bronze is a highly durable alloy, known for its excellent corrosion resistance and outstanding sliding properties
A high-performance nickel-chromium-based alloy known for its high strength properties and resistance to corrosion, oxidation, and high temperatures.
Stainless Steel 316 is a versatile and durable alloy known for its corrosion resistance, particularly in harsh environments
This cobalt-chromium alloy is known for its hardness, corrosion resistance, and ability to maintain performance in challenging environments.
Known for corrosion resistance, chemical and thermal shock resilience. Ideal for new components and repairs.
Industries benefiting from laser cladding
Topclad supplies laser-clad Inconel 625 solutions across high-performance sectors
Machine Parts
Food processing
Bridges & Water locks
Renewable Energy
Ready to talk
with us?
Topclad Laser Cladding is the leading manufacturer of innovative laser clad layers in Europe. Based in Lelystad, the Netherlands, Topclad Laser Cladding develops and applies laser clad layers for the most demanding industries including oil, gas, sustainable energy, offshore, dredging, mining, bridges and water locks, steel manufacturing and food processing.
"*" geeft vereiste velden aan
We are Topclad
Topclad is Europe’s leading manufacturer of innovative laser clad layers, based in Lelystad, the Netherlands. We specialize in developing and applying laser clad layers for the most demanding industries, including oil & gas, offshore, dredging, mining, bridges & water locks, steel manufacturing, and food processing.
Our mission is to provide components with superior protection against wear, corrosion, and impact, resulting in significantly improved reliability and uptime of capital-intensive equipment. With over 14 years of experience and a steadfast commitment to quality, we deliver solutions that enhance the performance and longevity of your critical machinery.
Why Topclad?
- Over 14 years laser cladding experience with over 10.000 cladded components
- More than 10 in-house developed laser clad layers
- Commitment to quality
- Expertise in comprehensive repairs
- 24.000 mm clad length capacity and 2.200 clad diameter capacity
- Chromium-6-free solutions