Stainless Steel 316
Stainless Steel 316 is a versatile and durable alloy known for its corrosion resistance, particularly in harsh environments. With its high chromium and molybdenum content, it is widely used in industrial applications where resistance to (chloride) corrosion is crucial, such as in the offshore, chemical, and food processing industries. Its robust performance against saltwater, acids, and other aggressive chemicals makes it a commonly used and all-round material for components.
What is Stainless Steel 316?
Stainless Steel 316 is a popular grade of stainless steel composed primarily of iron, chromium (16–18%), nickel (10–14%), and molybdenum (2–3%). The addition of molybdenum significantly enhances its corrosion resistance, especially against chlorides and other industrial chemicals. This alloy maintains its strength and toughness even at high temperatures, which is why it is frequently used in environments exposed to heat, moisture, and corrosive agents, such as seawater and acidic substances.
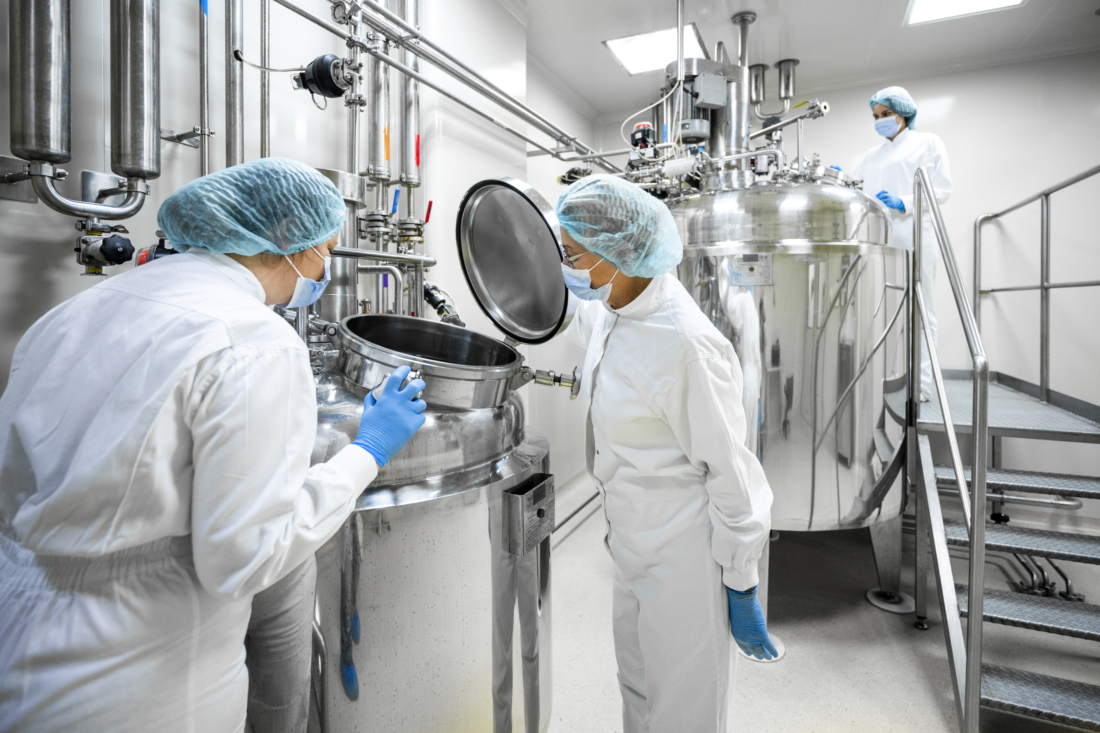
Chemical composition and classifications
316 stainless steel is also known under the following designations:
- AISI 316
- 1.4401 (EN)
- UNS S31600 (ASTM)
Typical chemical composition:
- Chromium (Cr): 16.5% – 18.5%
- Nickel (Ni): 10% – 13%
- Molybdenum (Mo): 2% – 2.5%
- Carbon (C): max 0.07%
- Iron (Fe): Balance
Variants of 316 include:
- 316L – low carbon version, better for welding
- 316H – high carbon, improved strength at elevated temperatures
- 316Ti – stabilised with titanium, excellent for high-temperature service
316 Stainless Steel is best suited for use in what type of environment?
- Offshore and marine: Components exposed to saltwater, including ship parts and underwater equipment
- Chemical processing: Tanks, valves, pipes, and heat exchangers in acidic or caustic environments
- Food and beverage processing: Surfaces and containers requiring hygiene and resistance to cleaning chemicals
- Water treatment and desalination: Pipes and structures exposed to chlorides and minerals
- Mining and heavy equipment: Hydraulic cylinders, protective housings, and wear components exposed to abrasive and corrosive media
- Construction in coastal zones: Facade systems, fasteners, and bridge elements exposed to marine atmosphere
Thanks to its robustness and corrosion resistance, 316 stainless steel remains a reliable material across a wide spectrum of industries.
Stainless Steel 316: key benefits & disadvantages
316 stainless steel offers a combination of key advantages for industrial use:
Benefits:
- Corrosion resistance: Solid resistance to pitting and crevice corrosion in chloride environments, making it suitable for marine and chemical settings.
- Strength and durability: High tensile and yield strength allow for long service life in mechanically demanding applications.
- Temperature resistance: Performs reliably at both high and low temperatures, including in cryogenic conditions.
- Hygienic properties: Non-reactive and easy to clean, making it compliant with strict sanitary requirements in food and pharma.
- Aesthetic finish: Often used where appearance matters, due to its clean, shiny surface.
Disadvantages:
Despite its strengths, stainless steel 316 has some limitations:
- Limited wear resistance: While corrosion-resistant, it does not perform well under extreme mechanical abrasion or impact. Overall, laser cladding by Topclad provides far better technical properties than Stainless Steel 316 pertaining to corrosion, wear, and chemical resistance.
- Less flexible for custom solutions: Cannot be tailored as easily as engineered coatings for highly specific performance demands.
- Heavier than coatings: In weight-critical applications, its bulk can be a drawback compared to high-performance overlays.
- Cost and availability: Stainless Steel 316 is not only more expensive than other stainless steel grades like 304 but also a less cost-effective choice than laser cladding. Topclad’s laser clad layers provide a cost-effective alternative to expensive stainless steel or duplex base materials. Components can be manufactured from much more affordable carbon steel, combined with an optimized Topclad laser clad layer. Carbon steel with a Topclad laser clad layer is not only more economical but also delivers shorter lead times and a longer service life.
Is 316 always the best choice?
316 stainless steel is often the default choice for challenging environments, but it’s not always the optimal one. In applications that require extreme wear resistance, precise surface engineering, or minimal maintenance, more advanced solutions may offer better performance.
For example, laser cladding can provide harder, thicker, and tailor-made coatings that outperform 316 in terms of lifespan and durability. In the next sections, we explore this technology and when it may be preferable.
What is the difference between 304 and 316 Stainless Steel?
The primary difference between Stainless Steel 304 and 316 lies in the addition of molybdenum in 316, which significantly enhances its resistance to chlorides and acidic environments. While 304 is a more cost-effective option and suitable for less corrosive environments, 316 is preferred for applications involving high exposure to saltwater, chemicals, and acids, making it the better choice for offshore and marine industries.
316 is preferred in environments where salt, moisture, or aggressive chemicals are present, while 304 suffices for general indoor or mild industrial applications.
Property | 304 Stainless Steel | 316 Stainless Steel |
---|---|---|
Corrosion resistance | Good | Excellent (due to Mo) |
Suitable for saltwater | No | Yes |
Cost | Lower | Higher |
Magnetic properties | Slightly magnetic after cold working | Non-magnetic |
Typical applications | Sinks, kitchen equipment, indoor architecture | Marine, pharma, chemical, food, heavy industry |
316L and other stainless steel 316 variants
- 316L: Low carbon version used for welded structures, to avoid carbide precipitation and intergranular corrosion.
- 316H: High carbon variant with improved strength at high temperatures, often used in pressure vessels and boilers.
- 316Ti: Titanium-stabilized alloy offering enhanced resistance to high-temperature corrosion, especially in cyclic conditions.
Each variant has its niche depending on thermal exposure, fabrication method, or mechanical requirement.
Alternative for 316 stainless steel
While stainless steel 316 is a trusted industrial material, it isn’t always the best solution for components that face extreme wear, localized corrosion, or require precise surface properties. In these situations, laser cladding offers a powerful alternative.
What is laser cladding?
Laser cladding is a precision surface engineering process in which a high-powered laser melts a coating material onto the surface of a component. The result is a metallurgically bonded layer with enhanced properties:
- Superior wear resistance
- Excellent corrosion protection
- Customizable thickness and material composition
- Minimal heat input and distortion
Unlike bulk materials like stainless steel, laser cladding applies only where needed — making it ideal for repairs, upgrades, or high-performance areas.
Why laser cladding is superior?
Compared to 316 stainless steel, laser cladding offers key advantages in:
- Performance: Longer lifespan in abrasive or corrosive environments
- Tailor ability: Engineered coatings for specific loads, media, or thermal cycles
- Cost-effectiveness: Lower lifecycle costs due to reduced maintenance and part replacement
It is especially effective for parts like hydraulic cylinders, offshore drilling components, and rollers, where high wear and precise tolerances are critical.
Industries benefiting from laser cladding
Topclad applies laser cladding in sectors where surface performance is mission-critical:
Machine Parts
Rollers & Drums
Other products in this serie
Aluminium bronze is a highly durable alloy, known for its excellent corrosion resistance and outstanding sliding properties
A high-performance nickel-chromium-based alloy known for its high strength properties and resistance to corrosion, oxidation, and high temperatures.
Stainless Steel 316 is a versatile and durable alloy known for its corrosion resistance, particularly in harsh environments
This cobalt-chromium alloy is known for its hardness, corrosion resistance, and ability to maintain performance in challenging environments.
Ready to talk
with us?
Topclad Laser Cladding is the leading manufacturer of innovative laser clad layers in Europe. Based in Lelystad, the Netherlands, Topclad Laser Cladding develops and applies laser clad layers for the most demanding industries including oil, gas, sustainable energy, offshore, dredging, mining, bridges and water locks, steel manufacturing and food processing.
"*" geeft vereiste velden aan
We are Topclad
Topclad is Europe’s leading manufacturer of innovative laser clad layers, based in Lelystad, the Netherlands. We specialize in developing and applying laser clad layers for the most demanding industries, including oil & gas, offshore, dredging, mining, bridges & water locks, steel manufacturing, and food processing.
Our mission is to provide components with superior protection against wear, corrosion, and impact, resulting in significantly improved reliability and uptime of capital-intensive equipment. With over 14 years of experience and a steadfast commitment to quality, we deliver solutions that enhance the performance and longevity of your critical machinery.
Why Topclad?
- Over 14 years laser cladding experience with over 10.000 cladded components
- More than 10 in-house developed laser clad layers
- Commitment to quality
- Expertise in comprehensive repairs
- 24.000 mm clad length capacity and 2.200 clad diameter capacity
- Chromium-6-free solutions