Laser cladding of ship propeller shafts by Topclad
Ship propeller shafts operate under extreme conditions, exposed to saltwater, abrasive materials, and high mechanical stress. Laser cladding offers a powerful solution for both new and worn-out propeller shafts, providing superior protection against wear and corrosion. Whether for newly manufactured shafts or repairs, laser cladding enhances durability, extending the lifespan of critical components. For these essential parts, it is crucial that they meet the strict standards set by a notified body. At Topclad, our Tardisphere layer is approved by Bureau Veritas, ensuring that our solutions comply with rigorous class-approved standards, giving you the reliability and certification required for maritime operations.
Maintenance and repair for ship propeller shafts
Over time, ship propeller shafts face significant wear and corrosion, which can lead to failure if not properly addressed. Laser cladding is an ideal solution for restoring damaged shafts to their original condition. By applying a protective layer, we can repair worn-out shafts, extending their operational life and improving their performance in demanding marine environments.
Our Tardisphere layer is frequently applied to bearing surfaces, as the sections where the bronze bearing sleeve rotates require enhanced wear resistance. Additionally, since these bearings are water-lubricated, the risk of corrosion is high. The Tardisphere layer provides both superior wear protection and corrosion resistance, ensuring that these critical areas withstand the harsh conditions they face.
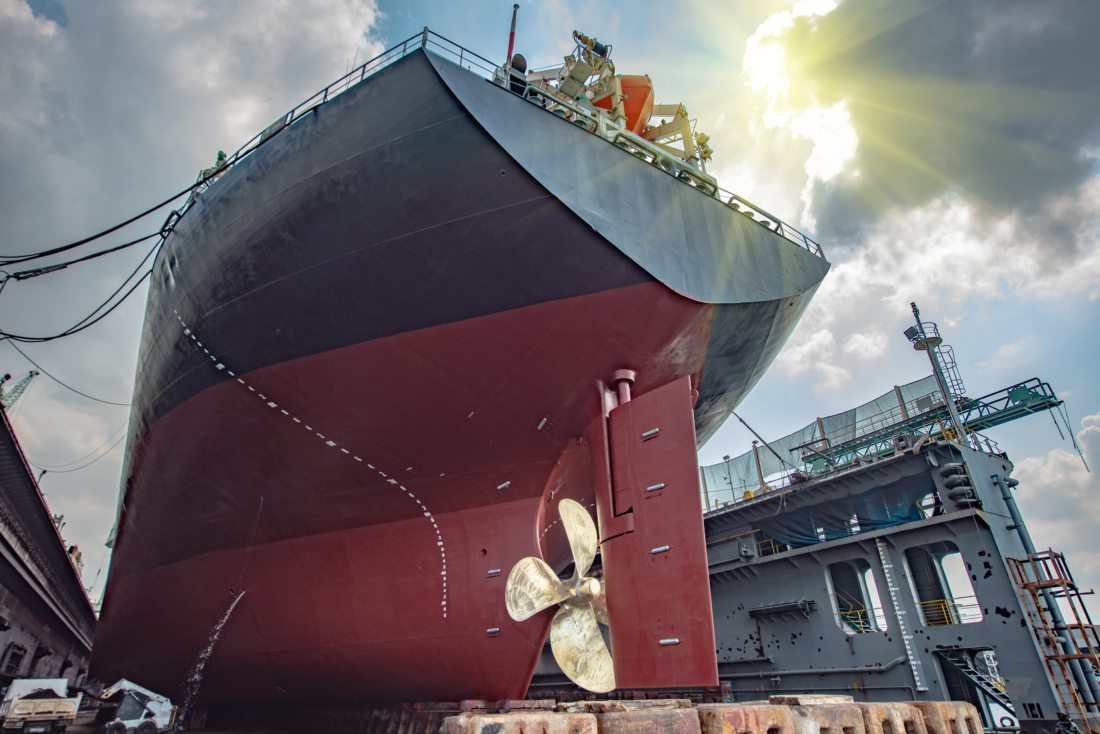
Laser cladding for ship components, the Netherlands
For assets managers as well as superintendents, seeking ship components repair-services, Topclad provides expert repair solutions designed to restore and enhance the performance of ship propeller shafts, thrusters shafts, rudders stocks and engine piston rods. Our cutting-edge laser cladding facility in Lelystad is equipped to handle ship components of various sizes, restoring them to optimal condition and extending their lifespan. With minimal lead time, our repairs ensure that your equipment returns to service quickly and reliably, making us the preferred choice for maritime products, either new or repairs.
Make your machines more reliable with laser cladding
To ensure your ship propeller shafts are ready for the rigors of maritime operations, invest in laser cladding from Topclad. With our advanced solutions, you can enhance the reliability and durability of your equipment while reducing maintenance costs and downtime. Request a quote today to learn how Topclad’s laser cladding can make a difference in your operations, or contact us for personalized advice and pricing information.
Laser clad layers for ship propellor shafts
Excellent corrosion and wear resistance, ideal for dredging and mining, or as a bearing surface.
Quarite NR provides the highest corrosion resistance in the Topclad portfolio, ideal for environments with extreme corrosion and moderate wear demands.
Quarite NR+ combines exceptional corrosion resistance (equal to NR) with enhanced wear resistance, making it perfect for harsh, most challenging environments.
Ready to talk
with us?
Topclad Laser Cladding is the leading manufacturer of innovative laser clad layers in Europe. Based in Lelystad, the Netherlands, Topclad Laser Cladding develops and applies laser clad layers for the most demanding industries including oil, gas, sustainable energy, offshore, dredging, mining, bridges and water locks, steel manufacturing and food processing.
"*" geeft vereiste velden aan
We are Topclad
Topclad is Europe’s leading manufacturer of innovative laser clad layers, based in Lelystad, the Netherlands. We specialize in developing and applying laser clad layers for the most demanding industries, including oil & gas, offshore, dredging, mining, bridges & water locks, steel manufacturing, and food processing.
Our mission is to provide components with superior protection against wear, corrosion, and impact, resulting in significantly improved reliability and uptime of capital-intensive equipment. With over 14 years of experience and a steadfast commitment to quality, we deliver solutions that enhance the performance and longevity of your critical machinery.
Why Topclad?
- Over 14 years laser cladding experience with over 10.000 cladded components
- More than 10 in-house developed laser clad layers
- Commitment to quality
- Expertise in comprehensive repairs
- 24.000 mm clad length capacity and 2.200 clad diameter capacity
- Chromium-6-free solutions