Stellite
Stellite is a cobalt-chromium alloy known for its hardness and corrosion resistance, to maintain long-term performances in extreme industrial environments. These alloys are typically used in applications where wear, corrosion, and temperature resistance are critical.
What is Stellite?
Stellite is primarily made of cobalt, chromium, and other elements such as tungsten or molybdenum. The cobalt base gives it resistance to wear and corrosion, while the chromium content provides protection against oxidation at high temperatures. Stellite is non-magnetic and retains its hardness and resistance even at elevated temperatures, making it highly valued in industries where components are exposed to related conditions.
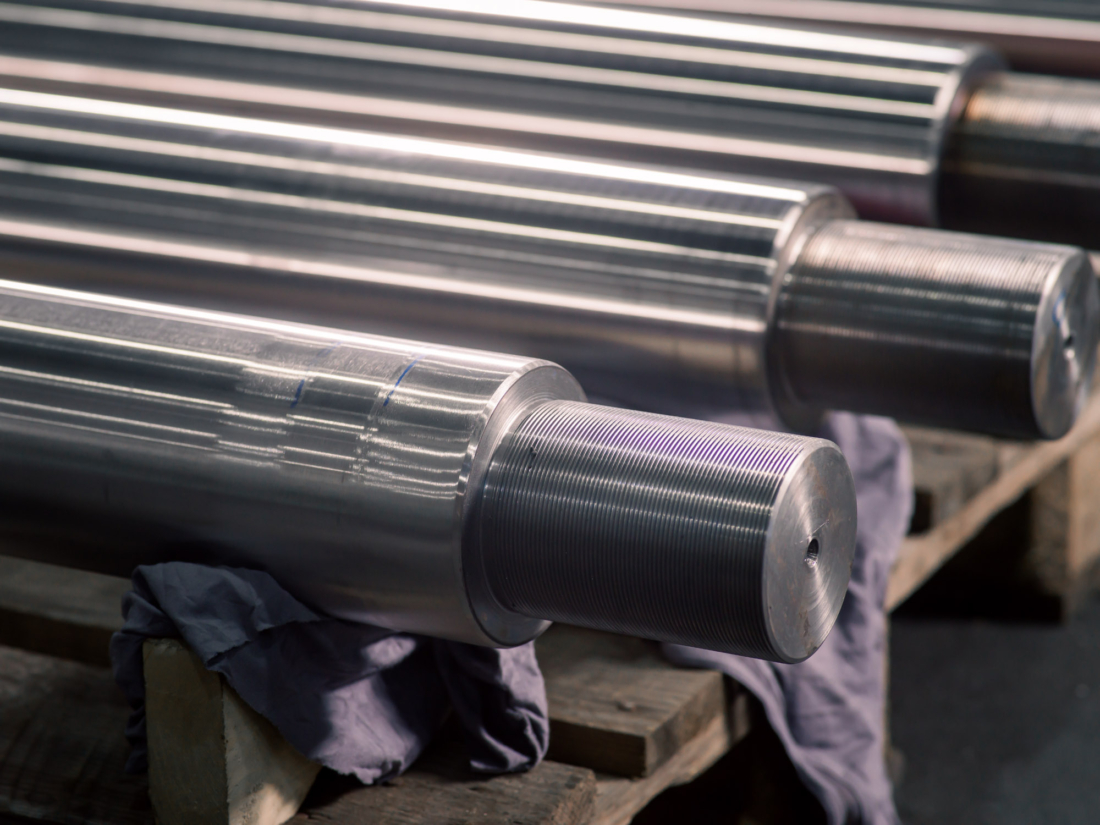
Stellite: Key Benefits & Disadvantages
Benefits:
- High temperature resistance: Stellite maintains its mechanical properties and hardness even at high temperatures, making it suitable for thermal applications.
- Corrosion resistance: Its chemical composition provides above average protection in corrosive environments, especially in the presence of seawater or chemicals.
- Wear resistance: Stellite is known for its hardness and wear resistance making it suitable for applications with abrasion or wear. However, field testing shows that the wear resistance of Stellite is not higher than that of Inconel 625.
Disadvantages:
- Machining difficulty: Its hardness, while beneficial in performance, makes Stellite difficult to machine and shape.
- Ductility: its limited ductility makes it prone to cracking or fracturing under high impact or dynamic loading conditions
- High cost: Stellite is significant more expensive compared to other materials like stainless steel or Inconel due to its complex manufacturing process and high market prices of its main element cobalt.
Stellite vs Inconel
Both Stellite and Inconel are used in high-temperature, corrosive environments, but they serve different purposes. Stellite is primarily valued for its hardness, especially at high temperatures. Inconel, on the other hand, has higher ductility and is more cost-effective while offering the same wear resistance, making it the preferred choice in markets such as offshore, dredging and high-pressure systems. Its combination of higher ductility, enhanced corrosion protection, and lower cost contributes to its frequent use in cylinder rods and high-pressure components, where flexibility and resilience under dynamic loads are essential.
What is Stellite used for?
Stellite is used in a variety of industries where extreme durability is required:
- Chemical Processing: Applied to equipment exposed to aggressive chemicals and severe mechanical stress.
- Oil and Gas: Suitable for valves, pumps, and bearings in abrasive and corrosive environments.
- Aerospace: Used in turbine blades and engine components due to its ability to withstand high temperatures and wear.
Markets & Applications
c
Steel industry
Machine Parts
Hydraulic Cylinder Rods
Rollers & Drums
Ready to talk
with us?
Topclad Laser Cladding is the leading manufacturer of innovative laser clad layers in Europe. Based in Lelystad, the Netherlands, Topclad Laser Cladding develops and applies laser clad layers for the most demanding industries including oil, gas, sustainable energy, offshore, dredging, mining, bridges and water locks, steel manufacturing and food processing.
"*" geeft vereiste velden aan
We are Topclad
Topclad is Europe’s leading manufacturer of innovative laser clad layers, based in Lelystad, the Netherlands. We specialize in developing and applying laser clad layers for the most demanding industries, including oil & gas, offshore, dredging, mining, bridges & water locks, steel manufacturing, and food processing.
Our mission is to provide components with superior protection against wear, corrosion, and impact, resulting in significantly improved reliability and uptime of capital-intensive equipment. With over 14 years of experience and a steadfast commitment to quality, we deliver solutions that enhance the performance and longevity of your critical machinery.
Why Topclad?
- Over 14 years laser cladding experience with over 10.000 cladded components
- More than 10 in-house developed laser clad layers
- Commitment to quality
- Expertise in comprehensive repairs
- 24.000 mm clad length capacity and 2.200 clad diameter capacity
- Chromium-6-free solutions