Introduction to Aluminium Bronze
Aluminium bronze is a highly durable alloy, known for its excellent corrosion resistance and outstanding sliding properties. It is widely used in applications such as bearing surfaces and pistons, where both friction reduction and protection against harsh environments are critical. Composed mainly of copper and aluminium, this alloy provides long-lasting performance under heavy mechanical loads and in corrosive conditions, making it a reliable choice for industries that demand durability and smooth operation.
What is Aluminium Bronze?
Aluminium Bronze is an alloy that typically consists of 9-12% aluminium combined with copper, often with small amounts of other elements like iron or nickel. This combination gives the alloy its high strength, superior sliding properties, and excellent corrosion resistance. Aluminium bronze is particularly valued for its ability to form a protective oxide layer, shielding it from further oxidation and corrosion, which makes it ideal for harsh environments like marine, aviation, and industrial settings.
The primary advantage of aluminium bronze lies in its friction-reducing and wear-resistant properties, making it a top choice for components that require smooth operation and durability under mechanical stress, such as pistons, and bearings. While its corrosion resistance is an added benefit, especially in water-lubricated applications like ship shafts, its main strength is its performance in applications that demand low friction and long-lasting wear resistance.
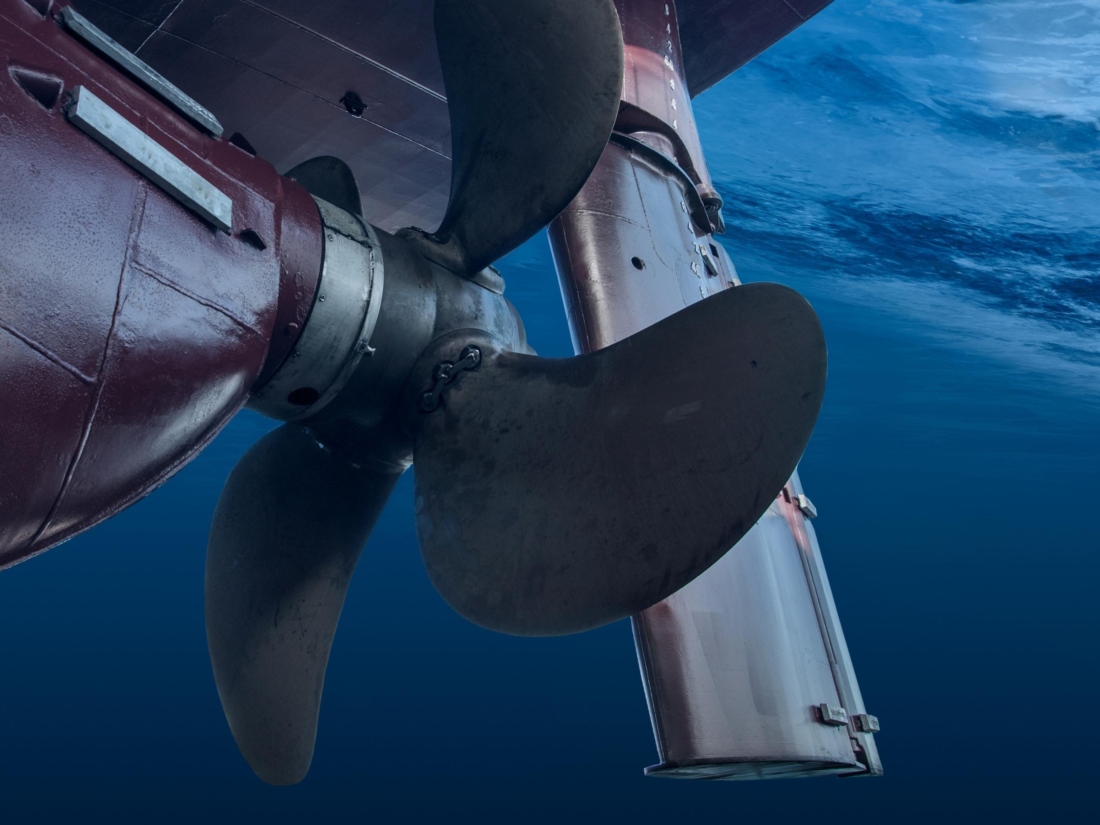
Key Benefits of Aluminium Bronze
The primary advantages of aluminium bronze are:
- Outstanding sliding properties, reducing friction and enhancing durability in high-load applications.
- Good corrosion resistance, particularly in water-lubricated environments, such as those in the maritime sector.
- High strength and wear resistance, enabling it to withstand mechanical stress and maintain performance in demanding conditions.
While aluminium bronze offers good corrosion resistance, its true strength lies in applications where friction reduction and wear resistance are the main priorities. In cases where extreme corrosion resistance or specific wear properties are required, other materials may be more suitable.
What is Aluminium Bronze Used For?
Aluminium bronze is mainly used in industries that require excellent sliding properties as well as corrosion resistance, such as:
- Marine applications: Bearings and valve components in water-lubricated environments, such as ship shafts.
- Pistons and bearing surfaces: Where low friction and durability under mechanical stress are crucial.
- Water-lubricated bearings: Especially in sectors like maritime and offshore industries.
Ready to talk
with us?
Topclad Laser Cladding is the leading manufacturer of innovative laser clad layers in Europe. Based in Lelystad, the Netherlands, Topclad Laser Cladding develops and applies laser clad layers for the most demanding industries including oil, gas, sustainable energy, offshore, dredging, mining, bridges and water locks, steel manufacturing and food processing.
"*" geeft vereiste velden aan
Other products in this serie
Aluminium bronze is a highly durable alloy, known for its excellent corrosion resistance and outstanding sliding properties
A high-performance nickel-chromium-based alloy known for its high strength properties and resistance to corrosion, oxidation, and high temperatures.
Stainless Steel 316 is a versatile and durable alloy known for its corrosion resistance, particularly in harsh environments
This cobalt-chromium alloy is known for its hardness, corrosion resistance, and ability to maintain performance in challenging environments.
Known for corrosion resistance, chemical and thermal shock resilience. Ideal for new components and repairs.
Examples of markets and applications
To discover how AluBronze or Topclad’s advanced laser cladding technology can help extend the lifespan of your equipment in corrosive environments and provide outstanding sliding properties, contact us today for personalized advice and a custom quote. Request a quote and find out how we can enhance the performance and durability of your critical components.
Ship Propellor Shafts
Machine Parts
We are Topclad
Topclad is Europe’s leading manufacturer of innovative laser clad layers, based in Lelystad, the Netherlands. We specialize in developing and applying laser clad layers for the most demanding industries, including oil & gas, offshore, dredging, mining, bridges & water locks, steel manufacturing, and food processing.
Our mission is to provide components with superior protection against wear, corrosion, and impact, resulting in significantly improved reliability and uptime of capital-intensive equipment. With over 14 years of experience and a steadfast commitment to quality, we deliver solutions that enhance the performance and longevity of your critical machinery.
Why Topclad?
- Over 14 years laser cladding experience with over 10.000 cladded components
- More than 10 in-house developed laser clad layers
- Commitment to quality
- Expertise in comprehensive repairs
- 24.000 mm clad length capacity and 2.200 clad diameter capacity
- Chromium-6-free solutions