Laser cladding for rollers & drums
Rollers and drums are crucial components used across various industries, including food processing, steel manufacturing, mining, and offshore operations. These parts are constantly exposed to abrasive materials, chemical fluids, high mechanical stress, temperature fluctuations, and corrosive environments.
Laser cladding offers a highly effective solution for both new and worn-out rollers and drums by applying a protective layer that enhances their durability and lifespan. For new products, laser cladding provides preventive protection, while worn-out parts can be restored to their original dimensions. With the added benefit of a metallurgical bond, there is no risk of layers detaching, making laser cladding a highly reliable option for critical components.
Typical properties and key considerations for rollers & drums
Each roller application comes with its own challenges: abrasive wear from conveyed materials, corrosion from aggressive environments, thermal cycling in casting lines, or mechanical stress from heavy loads. That’s why the choice of the protective coating must match the roller’s function, base material, and operating conditions. Here are some critical points:
- Wear Resistance: In industries like steel manufacturing, mining, and recycling, rollers are exposed to continuous friction and abrasive materials. Cladding solutions such as Tardisphere provide excellent wear resistance, ensuring a longer service life and reducing the need for frequent maintenance.
- Dimensional Integrity: Rollers and drums in industries like paper production or textiles must maintain precise dimensions to ensure smooth operation. Laser cladding is highly effective at restoring these components to their original dimensions without compromising the surface integrity, ensuring seamless functionality.
- Economic value of roller recovery: Industrial rollers are often highly customized and expensive to replace. Laser cladding offers a cost-effective solution by restoring worn surfaces instead of replacing entire components. This avoids high capital expenses and prevents costly downtime—making each repair a smart financial choice.
- Ecological advantage: reducing waste, extending lifecycle: Laser cladding restores rollers to their original dimensions, allowing full reuse of the existing base material. This reduces waste and emissions from producing new components. For companies aiming to operate more sustainably, it’s a practical and circular maintenance solution.
- Corrosion Resistance: In environments where rollers are exposed to corrosive fluids, such as in food processing or offshore operations, the Quarite-series offers superior corrosion resistance without the risk of peeling off. This ensures that the rollers maintain their integrity and performance, even in the harshest conditions. The metallurgical bonding of laser cladding ensures there’s no risk of loose particles contaminating food, making it an excellent solution for food-grade applications.
- Temperature Fluctuations: In applications where rollers and drums experience significant temperature changes, Topclad laser clad layers provide high thermal shock resistance, ensuring the materials retain their structural integrity under thermal stress.
- Chemical Resistance: Rollers in industries exposed to aggressive chemicals, like food processing and chemical manufacturing, benefit from the superior chemical resistance of the Quarite-series, protecting them against chemical substances without compromising their performance.
With tailored coatings like Tardisphere, the Quarite series and the Calduron series, we cover the full spectrum from dry abrasive loads to corrosive and thermally unstable environments.
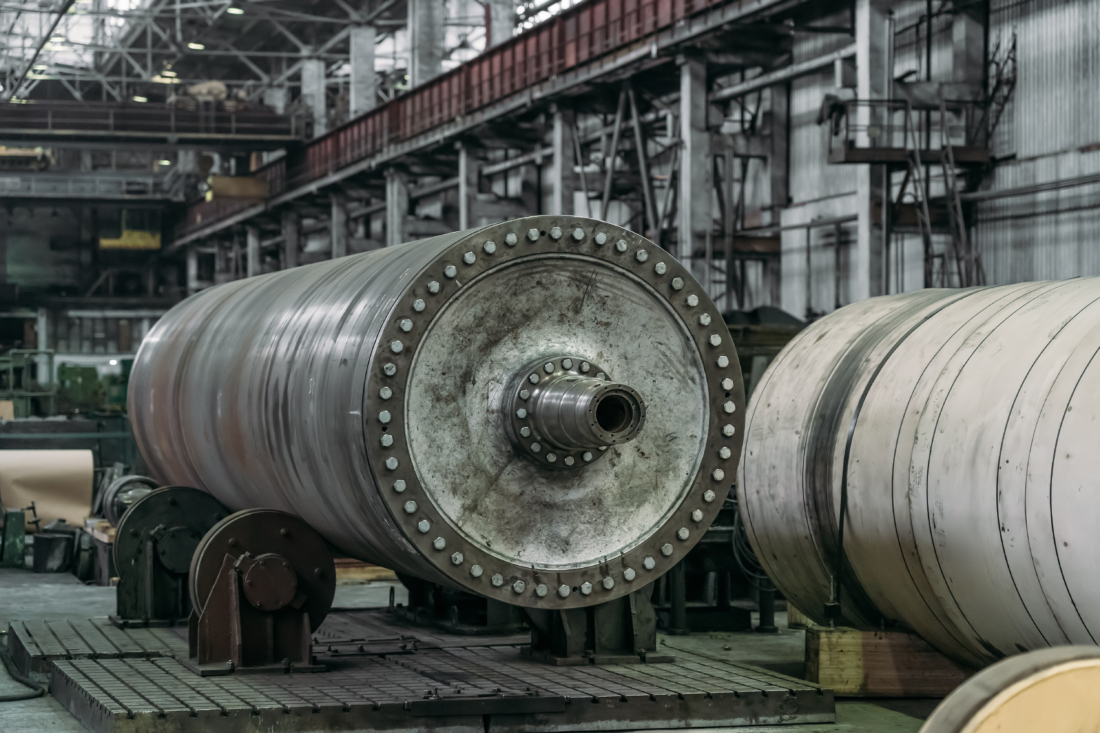
Typical applications
We apply laser clad coatings to both new and refurbished rollers and drums used in:
- Casting and hot rolling lines in the steel industry
- Conveyor drums and guide rollers in bulk handling
- Processing drums in the food and chemical industries
- Paper and pulp rollers exposed to moisture and abrasion
- Foil, film and textile rollers requiring surface stability
From 50 cm to >20 meters in length, we protect rollers in every shape and function.
Maintenance and repair for rollers & drums
Over time, rollers and drums experience significant wear and corrosion due to constant friction and exposure to harsh environments. For instance, in industries like food processing, where aggressive lyes and acids are frequently used, chemical resistance becomes crucial. Quarite N is an ideal solution for these environments due to its exceptional protection against chemical attack. The metallurgical bonding of laser cladding eliminates the risk of loose particles contaminating food, making it an excellent choice for food-grade applications.
Often, the bearing surfaces endure the most wear due to high mechanical loads and continuous rotation. Applying Topclad’s Tardisphere layer reinforces these critical areas with both wear and corrosion resistance, significantly extending their durability. Additionally, laser cladding can restore bearing surfaces and other roller/drum areas to their original dimensions with precision, enhancing overall product performance.
Beyond just repairing bearing surfaces, cladding the entire roller or drum provides greater benefits. Given the size, weight, and intrinsic value of these components—up to 60 tons and 2200 mm in diameter—laser cladding is a cost-effective solution for protecting new products and restoring worn-out parts to their original specifications. This approach not only reduces the risk of breakdowns but also extends the equipment’s operational life, making it a preventive improvement by upgrading the material properties beyond the original.
Advantages of Topclad’s repair approach include:
- Short lead times – Fast turnaround with minimal disruption
- Material savings – No need for complete roller replacement
- Repeatability – Cladded surfaces can be reapplied multiple times
- Dimensional precision – Tight tolerances maintained
- Sustainability – Less material use and extended component life
Whether it’s preventive maintenance or urgent repair, we keep your rollers running.
Laser clad layers for rollers & drums
Stainless Steel 316 is a versatile and durable alloy known for its corrosion resistance, particularly in harsh environments
Sinex replaces full material stainless steel with a laser clad layer on carbon steel, matching 316L's properties.
Optimized for many applications, Quarite N offers excellent corrosion resistance and strong chemical & thermal propertie
Quarite NR provides the highest corrosion resistance in the Topclad portfolio, ideal for environments with extreme corrosion and moderate wear demands.
Quarite NR+ combines exceptional corrosion resistance (equal to NR) with enhanced wear resistance, making it perfect for harsh, most challenging environments.
Specially developed to combine the best of both worlds—excellent corrosion resistance and high wear resistance—without using carbides.
Proven performance in the steel industry
Few industries put more stress on rollers than steel production. In continuous casting and hot rolling, rollers are exposed to extreme heat, mechanical loads, cooling water and abrasive contact with semi-finished steel. Traditional overlay techniques like submerged arc welding with martensitic stainless steels often suffer from rapid corrosion, cracking or early failure.
Topclad’s Calduron series was developed specifically for such conditions. It delivers high thermal fatigue strength, corrosion resistance and wear protection, without requiring pre- or post-heat treatment. Already validated by leading steel producers, Calduron ensures maximum uptime, longer roll life, and improved safety in casting environments.
Topclad’s expertise in rollers & drums
At Topclad, we offer customized laser cladding solutions for rollers and drums, tailored to meet the specific needs of your industry. Our cutting-edge technology creates a metallurgical bond with the base material, ensuring a long-lasting and reliable solution. Whether for new or existing components, laser cladding is a proven method for maximizing the performance of your rollers and drums while minimizing downtime.
Learn more about our laser cladding solutions and contact us today to discover how Topclad can extend the life of your rollers and drums with our advanced technology. Request a quote to start optimizing your operations with Topclad’s expertise.
Markets
Laser cladding for rollers & drums is used in these industries:
Ready to talk
with us?
Topclad Laser Cladding is the leading manufacturer of innovative laser clad layers in Europe. Based in Lelystad, the Netherlands, Topclad Laser Cladding develops and applies laser clad layers for the most demanding industries including oil, gas, sustainable energy, offshore, dredging, mining, bridges and water locks, steel manufacturing and food processing.
"*" geeft vereiste velden aan
We are Topclad
Topclad is Europe’s leading manufacturer of innovative laser clad layers, based in Lelystad, the Netherlands. We specialize in developing and applying laser clad layers for the most demanding industries, including oil & gas, offshore, dredging, mining, bridges & water locks, steel manufacturing, and food processing.
Our mission is to provide components with superior protection against wear, corrosion, and impact, resulting in significantly improved reliability and uptime of capital-intensive equipment. With over 14 years of experience and a steadfast commitment to quality, we deliver solutions that enhance the performance and longevity of your critical machinery.
Why Topclad?
- Over 14 years laser cladding experience with over 10.000 cladded components
- More than 10 in-house developed laser clad layers
- Commitment to quality
- Expertise in comprehensive repairs
- 24.000 mm clad length capacity and 2.200 clad diameter capacity
- Chromium-6-free solutions