Traditional surface treatment methods
Traditional surface treatments and surface coatings have long been the standard for industries seeking corrosion protection and wear resistance for critical components. These methods, including hard chrome plating, ceramic coating, nickel-chrome plating, and thermal spray techniques such as HVOF spraying, are widely used to extend the lifespan of industrial equipment. However, each of these methods comes with limitations, such as poor bonding, porosity, and environmental impact.
Laser cladding advantages
Laser cladding, on the other hand, solves many of these issues by creating a metallurgical bond between the base material and the coating. This results in a denser, non-porous, and highly wear-resistant layer making it ideal for challenging environments and applications. Laser cladding’s costs are steadily decreasing, making it ideal not only for heavy-duty applications but also increasingly for lighter industrial needs. As a result, laser cladding not only increases durability but also reduces maintenance requirements and lowers the total cost of ownership (TCO) for critical components.
On this page, we provide a concise introduction to each technique. For a more information about the differences with and benefits of laser cladding’s, visit our laser cladding comparison page or contact us directly.
The most common traditional methods can be categorized as:
Galvanic Treatments
Thermal Spraying Methods
Other
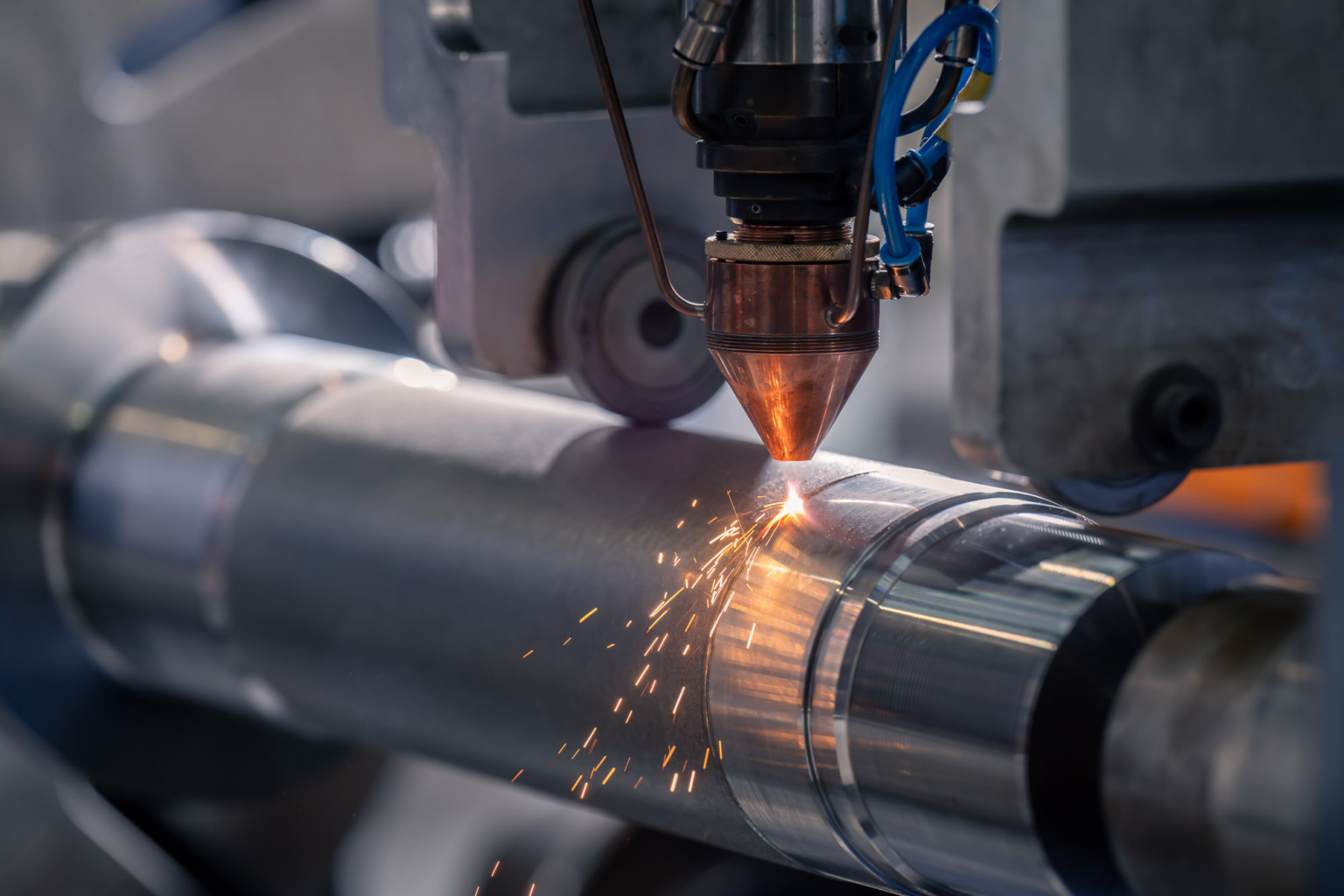
What is Hard Chrome Plating?
Hard chrome plating involves electroplating a thin layer of chromium onto metal surfaces, enhancing wear and corrosion resistance for applications like hydraulic cylinders and rollers. However, despite its widespread use in industries such as manufacturing or offshore, hard chrome plating is known to have several key weaknesses in demanding environments. The chromium layer is mechanically bonded, which can lead to poor adhesion and cracking under heavy loads or temperature fluctuations. Although hard chrome provides a tough outer layer, it is brittle and susceptible to peeling or flaking when subjected to impact or continuous mechanical stress, limiting its durability in demanding environments.
Hard chrome plating is also vulnerable to pitting and rust formation when exposed to moisture, particularly when the protective oil layer on cylinder rods is missing due to lack of movement, exposing the plated surface to the elements. Additionally, this process involves hexavalent chromium (Cr6). Chromium-6 is a chemical commonly used in various industrial coatings, but it is associated with serious health risks. As a result, the European Commission has significantly restricted its use, and a complete ban is expected to be imposed following the current regulations. While hard chrome can last several years under moderate conditions, it often requires frequent maintenance, such as reapplication and polishing, to maintain its protective properties in more aggressive settings.
What is Nickel-Chrome Plating?
Nickel-chrome plating combines a nickel base layer with a chromium top layer to provide a shiny, corrosion-resistant finish, commonly used for diverse industrial components like piston rods and valves. Although NiCr plating offers moderate corrosion resistance, it has limitations in high-stress or corrosive environments such as those encountered in oil & gas, marine, and heavy machinery industries.
Under harsh conditions, microcracks often develop in the nickel-chrome layer, allowing moisture and chemicals to penetrate the surface, leading to corrosion beneath the coating. This is particularly problematic in hydraulic cylinder rods, where long exposure to outdoor environments without a protective oil film can accelerate corrosion and wear. Due to its porous nature, NiCr does not provide a fully sealed surface, leaving the base material susceptible to damage over time, which can necessitate costly repairs or replacements.
What is Thermal Spraying?
Thermal spraying refers to a family of processes where heated or molten materials are sprayed onto a surface to create a protective coating. Used across industries such as aerospace and power generation, thermal spraying can apply coatings made of alloys, ceramics, and composites. The primary advantage of thermal spraying is its versatility, as it can coat large surface areas with relatively thick layers. However, thermal spray coatings, including plasma spraying, are typically mechanically bonded to the substrate, which means they lack the metallurgical bond that laser cladding provides. This makes them more prone to cracking, chipping, and delamination, particularly under heavy mechanical loads or thermal cycling.
While thermal spray coatings can provide excellent resistance in certain conditions, their porosity limits their effectiveness in highly corrosive environments where moisture and chemicals can penetrate, leading to potential corrosion of the underlying material. Additionally, in applications where components are exposed to both high temperatures and mechanical stress, thermal spray coatings may deteriorate more quickly than expected. Frequent inspections are essential to detect any wear or damage early on, as damaged coatings require recoating to maintain adequate protection.
What is HVOF Spraying?
HVOF (High-Velocity Oxygen Fuel) spraying is a specific type of thermal spraying known for producing dense, hard coatings that are widely used in industries like aerospace, oil & gas, and heavy machinery. HVOF provides excellent wear resistance, especially in abrasive and corrosive environments. However, despite its hardness, HVOF relies on mechanical bonding, which makes it vulnerable to delamination and microcracks under high impact or fluctuating temperatures. Also, the porous nature of HVOF limits its corrosion protection, and is therefore less suitable for aggressive corrosive environments. In applications such as hydraulic cylinders and pump shafts, HVOF can require periodic reapplication to address wear or damage, which can become costly over time.
HVOF coatings have a relatively long lifespan in controlled environments but are prone to cracking when exposed to sudden impact or thermal cycling. Regular inspection and repair are needed to ensure consistent performance, as damage from cracking or delamination compromises the protective qualities of the coating.
What is Plasma Spraying?
Plasma spraying is a thermal spray process using a high-temperature plasma jet to melt and deposit materials onto surfaces. It is widely used for ceramic, metallic, and composite coatings in industries such as aerospace, automotive, and power generation. Plasma spraying is versatile, but like other thermal spray techniques, it relies on a mechanical bond that is prone to delamination under mechanical stress or temperature cycling.
In high-stress applications like turbine blades or engine components, plasma-sprayed coatings may crack or peel over time, especially if exposed to impact, vibration, or temperature fluctuations. The porous nature of many plasma-sprayed coatings also limits their corrosion protection, making regular maintenance and recoating necessary to maintain their effectiveness in aggressive environments.
What is Ceramic Coating?
Ceramic coatings are known for their high-temperature resistance and are frequently applied in aerospace and automotive components, such as exhaust systems and turbines. These coatings can withstand extreme heat, serving as thermal barriers that protect parts like engine parts and exhaust systems. However, ceramic coatings are less effective under mechanical stress and impact resistance, making them vulnerable to cracking and chipping when subjected to physical wear or vibration.
In applications where components are exposed to both high temperatures and physical stress, ceramic coatings can become brittle, making them susceptible to cracking and chipping. Their inherently porous structure, especially in black coatings, further increases their sensitivity to fractures. The mechanical bonding of ceramic layers to the substrate leaves them vulnerable to delamination under impact or vibration. In high-load environments, this vulnerability often exposes the base material to wear and corrosion, necessitating frequent reapplication or repair to maintain protection. Industries like mining or heavy equipment manufacturing may find ceramic coatings insufficient for long-term durability under abrasive conditions.
What is Plasma Transfer Arc?
Plasma Transfer Arc (PTA) is an advanced surface enhancement technique used to apply durable, wear-resistant coatings to metal surfaces. Utilizing a high-energy plasma arc, the PTA process melts a metallic powder or wire, creating a metallurgical bond with the substrate for a robust, long-lasting layer. Known for its strength and durability, PTA coatings are particularly suited for applications in demanding industries like oil and gas, mining, and heavy machinery,
where components are exposed to extreme wear and require exceptional protection. Although PTA provides a resilient coating, the higher heat input can lead to a broader heat-affected zone, potentially causing thermal stress or distortion in thinner materials. Additionally, PTA is typically more suited to creating thicker layers, which may lead to increased material use and less precision when applying fine or uniform coatings.
Traditional surface treatments vs laser cladding
Unlike traditional methods, laser cladding provides a metallurgical bond for stronger adhesion and offers superior wear resistance and corrosion protection without the porosity issues seen in NiCr and HVOF. While initial costs may be higher, laser cladding results in significant long-term savings by reducing the need for frequent repairs and replacements. Laser cladding is also increasingly suitable for a range of applications as costs decrease, making it an excellent alternative to traditional coatings for both heavy-duty and lighter industrial uses.