Laser cladding repair
Laser cladding repair is a highly effective method for restoring worn or damaged industrial components without the need for full replacement. At Topclad, we use advanced laser-based techniques to apply wear-resistant, corrosion-proof coatings that return your components to original or even improved specifications. Whether you’re dealing with hydraulic cylinder rods, rollers, shafts, or high-value components, laser cladding offers a fast, economical, and durable repair solution. Over the years, we’ve helped customers across industries—from offshore and mining to heavy manufacturing—extend the life of such high-value part. If you’re looking for a cost-efficient and durable repair solution, laser cladding may be exactly what you need.
What is laser cladding repair?
Laser cladding repair is a precision technique where a protective high quality alloy is applied to a damaged or worn surface using a high-powered laser. The result is a metallurgical bond between the base material and the new layer—far stronger than traditional mechanical coatings or mechanical overlays. Unlike traditional coatings or thermal sprays, laser cladding forms a true metallurgical bond with the base material, offering superior durability, corrosion resistance and thickness control.
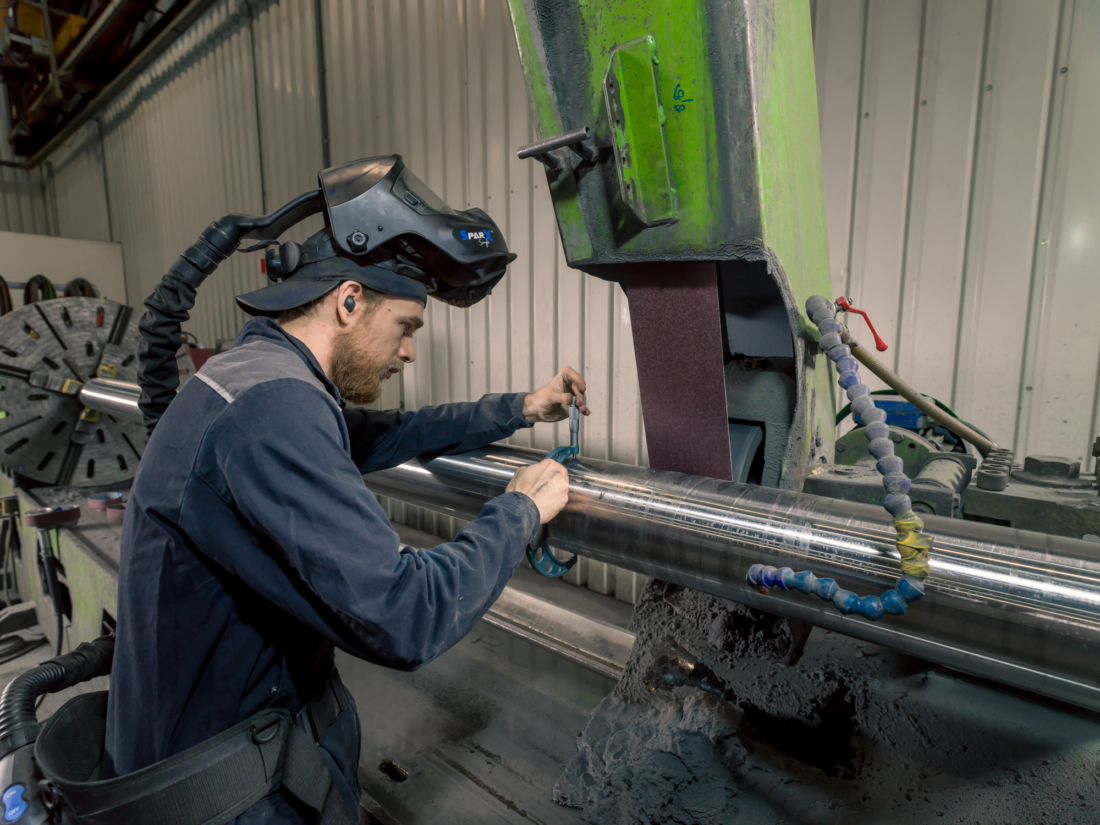
Benefits of laser cladding repair at a glance
- Save up to 70% compared to full replacement
- Minimize downtime with fast repairs
- Restore components to original dimensions with thick, fully bonded layers
- Extend the lifetime of critical equipment
All of the benefits?
Learn more about all of the advantages of laser claddingAt Topclad, we apply laser cladding in three different repair methods, depending on the wear pattern and application.
Full-surface restoration with uniform thickness
We rebuild the entire component surface with a uniform laser-clad layer. This is ideal when general wear or corrosion has affected the full length of the part, such as hydraulic rods or shafts.
Full-surface restoration with local reinforcement
We selectively apply more material in areas with heavier corrosion or wear — such as shaft ends that are constantly exposed. These zones are pre-machined deeper, allowing us to build back more thickness locally while keeping the rest of the part optimally dimensioned. This method saves both time and material, while extending component life.
Localized repair with TIG equipment
For smaller surface damages, our customers can carry out touch-up repairs themselves using standard TIG welding machines — no disassembly required. It’s a fast, efficient solution for minor (impact) damages. For larger or more complex repairs, components are sent to our facility for full restoration.
Typical repair applications
Over the years, we’ve successfully restored components in industries like mining, offshore, and heavy manufacturing. We apply laser cladding repair in a wide range of high-performance applications where precision and durability are critical, including:
- Hydraulic cylinders and piston rods: Repairing corrosion damage and wear caused by heavy duty operation
- Rollers and drums: In food and steel industries, where abrasive wear or chemical exposure damages the surface
- Shafts and axles: Including ship propeller shafts, drive shafts, and rotating equipment in maritime and industrial settings
- Machine components – Such as shafts and pistons exposed to mechanical wear, impact or corrosion in harsh environments
In every case, we tailor the coating material and thickness to the specific stress and wear profile of your application. Where corrosion has significantly degraded the surface — either by pitting, weakening or eroding — we restore the part with a custom-built laser clad layer.
Unlike conventional spray coatings such as HVOF or hard chrome, laser cladding allows for thicker layers without the risk of cracking or delamination under stress, bending or impact. This makes it a more reliable choice for critical components that operate in corrosive or heavy duty environments.
Why choose laser cladding over replacement or conventional repair?
Laser cladding outperforms HVOF or hard chrome coatings in wear life, bond strength, and design flexibility. Compared to HVOF spraying or thermal coatings, laser cladding offers:
- Corrosion-focused restoration – Laser cladding is ideal for repairing corrosion damage, rebuilding material with a protective, bonded alloy
- Thick layer capability – Unlike HVOF or NiCr coatings, our layers can be applied up to several millimeters thick without cracking or delaminating
- Cost-effective – Only the affected zone is rebuilt; no full component replacement needed
- Fast turnaround – Thanks to our in-house capacity and efficient processes, we offer short lead times for urgent repairs.
- Performance upgrade – We can improve the surface beyond original spec with engineered alloys
- Sustainable – Less material use, lower carbon footprint, Chromium-6-free coatings
- Repeatable – Components can be restored repeatedly without replacing the base material.
The laser cladding repair process
If your component needs a full repair, here’s what we’ll do—step by step—to get you back up and running:
- Inspection – We assess the type, depth, and cause of the damage.
- Surface preparation – For full rebuild: we remove the old layer with precision turning.
- Cladding – We apply a high-performance alloy (e.g., Inconel 625, Quarite, Tardisphere) in layers of 0,225 mm to >10mm if needed, matched to your needs.
- Post-processing – We machine and polish the surface back to the required specifications.
Industries that benefit from laser cladding repair
Topclad serves a wide range of sectors where reliability, uptime, and precision are paramount:
How can we help you?
Our extensive experience and control over our processes make Topclad a leader in providing dependable, high-quality surface treatments for industries requiring the utmost precision and reliability.
Curious about how Topclad can elevate your business with advanced laser cladding solutions? Visit our laser cladding applications page for detailed insights into our capabilities for your application and our success stories.
Laser Clad Layers
Price information
We are Topclad
Topclad is Europe’s leading manufacturer of innovative laser clad layers, based in Lelystad, the Netherlands. We specialize in developing and applying laser clad layers for the most demanding industries, including oil & gas, offshore, dredging, mining, bridges & water locks, steel manufacturing, and food processing.
Our mission is to provide components with superior protection against wear, corrosion, and impact, resulting in significantly improved reliability and uptime of capital-intensive equipment. With over 14 years of experience and a steadfast commitment to quality, we deliver solutions that enhance the performance and longevity of your critical machinery.
Why Topclad?
- Over 14 years laser cladding experience with over 10.000 cladded components
- More than 10 in-house developed laser clad layers
- Commitment to quality
- Expertise in comprehensive repairs
- 24.000 mm clad length capacity and 2.200 clad diameter capacity
- Chromium-6-free solutions
Ready to talk
with us?
Topclad Laser Cladding is the leading manufacturer of innovative laser clad layers in Europe. Based in Lelystad, the Netherlands, Topclad Laser Cladding develops and applies laser clad layers for the most demanding industries including oil, gas, sustainable energy, offshore, dredging, mining, bridges and water locks, steel manufacturing and food processing.
"*" geeft vereiste velden aan