Traditionele methoden voor oppervlaktebehandeling
Traditionele oppervlaktebehandelingen en -coatings zijn lang de standaard geweest voor industrieën die op zoek zijn naar corrosiebescherming en slijtvastheid voor kritieke onderdelen. Deze methoden, waaronder hardverchroming, keramische coating, nikkel-chroomplating en thermische spuittechnieken zoals HVOF-spuiten, worden veel gebruikt om de levensduur van industriële apparatuur te verlengen. Elk van deze methoden heeft echter zijn beperkingen, zoals slechte hechting, poreusheid en milieueffecten.
Voordelen van lasercladding
Lasercladding daarentegen lost veel van deze problemen op door een metallurgische verbinding te creëren tussen het basismateriaal en de coating. Dit resulteert in een dichtere, niet-poreuze en zeer slijtvaste laag die ideaal is voor veeleisende omgevingen en toepassingen. De kosten van lasercladding dalen gestaag, waardoor het niet alleen ideaal is voor zware toepassingen, maar ook steeds meer voor lichtere industriële toepassingen. Als gevolg hiervan verhoogt lasercladding niet alleen de duurzaamheid, maar vermindert het ook de onderhoudsvereisten en verlaagt het de totale eigendomskosten (TCO) voor kritieke componenten.
Op deze pagina geven we een beknopte introductie van elke techniek. Ga voor meer informatie over de verschillen met en voordelen van lasercladding naar onze vergelijkingspagina voor lasercladding of neem direct contact met ons op.
De meest voorkomende traditionele methoden kunnen worden gecategoriseerd als:
Galvanische behandelingen
Thermische spuitmethoden
Andere
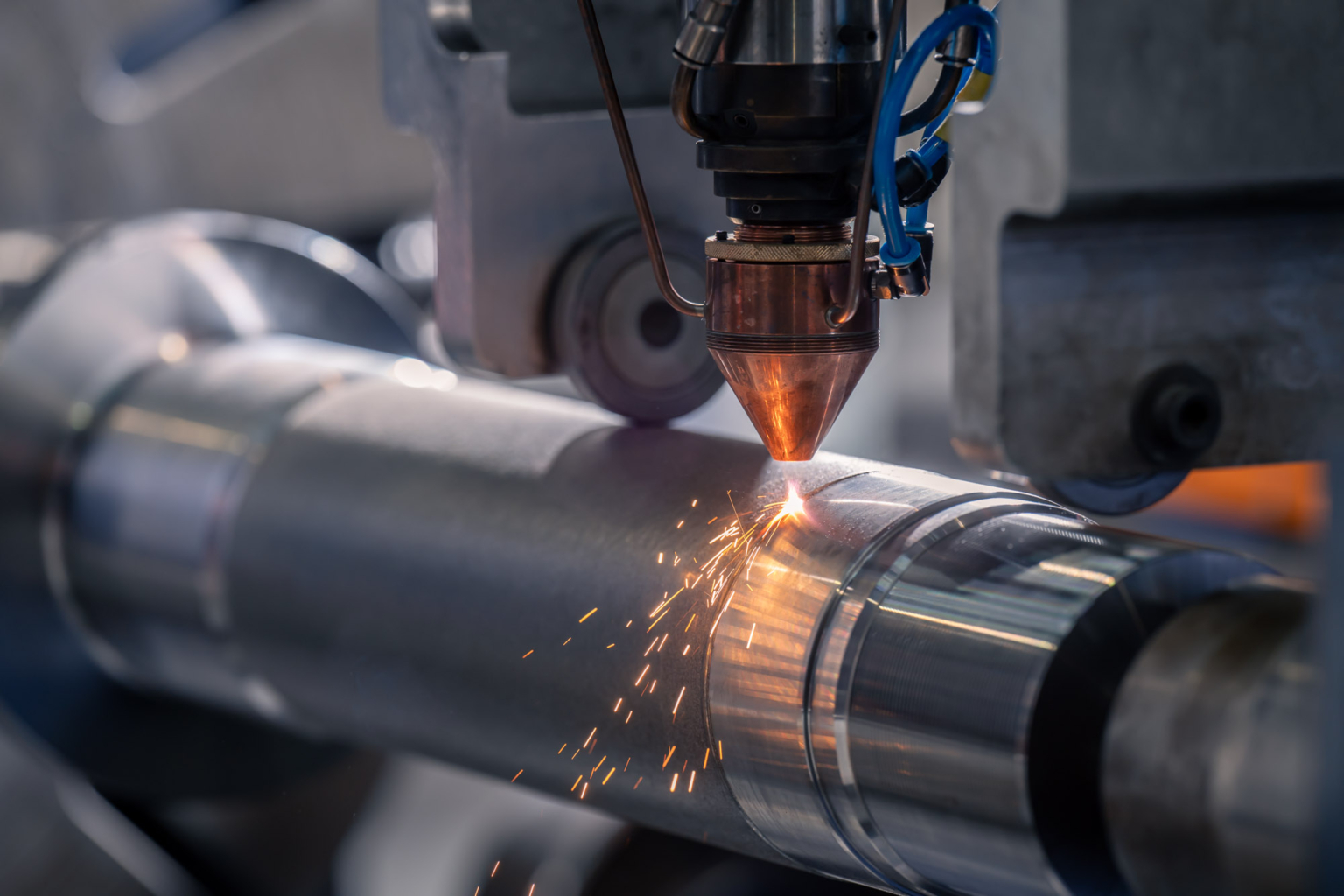
Wat is hardverchromen?
Bij hardverchromen wordt een dunne laag chroom elektrolytisch op metalen oppervlakken aangebracht, waardoor de slijtage- en corrosiebestendigheid voor toepassingen als hydraulische cilinders en rollen wordt verbeterd. Ondanks het wijdverbreide gebruik in industrieën zoals productie of offshore, staat hardverchromen er echter om bekend een aantal belangrijke zwakke punten te hebben in veeleisende omgevingen. De chroomlaag is mechanisch gebonden, wat kan leiden tot slechte hechting en scheuren onder zware belasting of temperatuurschommelingen. Hoewel hardchroom een taaie buitenlaag vormt, is het bros en gevoelig voor afschilferen of afschilferen wanneer het wordt blootgesteld aan schokken of voortdurende mechanische spanning, waardoor de duurzaamheid in veeleisende omgevingen wordt beperkt.
Hardverchroming is ook kwetsbaar voor pitting en roestvorming wanneer het wordt blootgesteld aan vocht, vooral wanneer de beschermende olielaag op cilinderstangen ontbreekt door gebrek aan beweging, waardoor het geplateerde oppervlak wordt blootgesteld aan de elementen. Bovendien is bij dit proces zeswaardig chroom (Cr6) betrokken. Chroom-6 is een chemische stof die vaak wordt gebruikt in verschillende industriële coatings, maar het wordt in verband gebracht met ernstige gezondheidsrisico's. Als gevolg hiervan heeft de Europese Commissie het gebruik ervan aanzienlijk beperkt en er wordt een volledig verbod verwacht na de huidige regelgeving. Hoewel hardchroom onder gematigde omstandigheden meerdere jaren kan meegaan, is er vaak frequent onderhoud nodig, zoals opnieuw aanbrengen en polijsten, om de beschermende eigenschappen in agressievere omgevingen te behouden.
Wat is vernikkelen?
Bij nikkel-chroomplateren wordt een nikkelbasislaag gecombineerd met een chroomtoplaag om een glanzende, corrosiebestendige afwerking te verkrijgen die vaak wordt gebruikt voor diverse industriële onderdelen zoals zuigerstangen en kleppen. Hoewel NiCr-plateren een matige corrosieweerstand biedt, heeft het zijn beperkingen in omgevingen met hoge druk of corrosie, zoals in de olie- en gasindustrie, de scheepvaart en de industrie voor zware machines.
Onder zware omstandigheden ontstaan er vaak microscheurtjes in de nikkel-chroomlaag, waardoor vocht en chemicaliën het oppervlak kunnen binnendringen, wat leidt tot corrosie onder de coating. Dit is vooral problematisch bij hydraulische cilinderstangen, waar langdurige blootstelling aan buitenomgevingen zonder beschermende oliefilm corrosie en slijtage kan versnellen. Door zijn poreuze aard biedt NiCr geen volledig afgedicht oppervlak, waardoor het basismateriaal na verloop van tijd vatbaar is voor schade, wat dure reparaties of vervangingen noodzakelijk kan maken.
Wat is thermisch spuiten?
Thermisch spuiten verwijst naar een reeks processen waarbij verwarmde of gesmolten materialen op een oppervlak worden gespoten om een beschermende coating aan te brengen. Thermisch spuiten wordt gebruikt in industrieën zoals lucht- en ruimtevaart en energieopwekking en kan coatings aanbrengen van legeringen, keramiek en composieten. Het belangrijkste voordeel van thermisch spuiten is de veelzijdigheid, omdat grote oppervlakken met relatief dikke lagen kunnen worden bedekt. Thermische spuitcoatings, inclusief plasmaspuiten, zijn echter meestal mechanisch gebonden aan het substraat, wat betekent dat ze niet de metallurgische binding hebben die lasercladding biedt. Hierdoor zijn ze vatbaarder voor barsten, afschilferen en delaminatie, vooral onder zware mechanische belastingen of thermische cycli.
Hoewel thermische spuitcoatings uitstekende weerstand kunnen bieden in bepaalde omstandigheden, beperkt hun poreusheid hun doeltreffendheid in zeer corrosieve omgevingen waar vocht en chemicaliën kunnen binnendringen, wat kan leiden tot corrosie van het onderliggende materiaal. Bovendien kunnen thermische spuitcoatings in toepassingen waar onderdelen worden blootgesteld aan zowel hoge temperaturen als mechanische belasting, sneller verslechteren dan verwacht. Regelmatige inspecties zijn essentieel om slijtage of schade in een vroeg stadium op te sporen, aangezien beschadigde coatings opnieuw moeten worden gecoat om voldoende bescherming te blijven bieden.
Wat is HVOF-spuiten?
HVOF (High-Velocity Oxygen Fuel) spuiten is een specifiek type thermisch spuiten dat bekend staat om het produceren van dichte, harde coatings die veel worden gebruikt in industrieën zoals lucht- en ruimtevaart, olie & gas en zware machines. HVOF biedt een uitstekende slijtvastheid, vooral in schurende en corrosieve omgevingen. Ondanks de hardheid is HVOF echter afhankelijk van mechanische hechting, waardoor het kwetsbaar is voor delaminatie en microscheurtjes bij grote schokken of wisselende temperaturen. Ook beperkt de poreuze aard van HVOF de corrosiebescherming, waardoor het minder geschikt is voor agressieve corrosieve omgevingen. In toepassingen zoals hydraulische cilinders en pompassen kan het nodig zijn HVOF periodiek opnieuw aan te brengen om slijtage of schade aan te pakken, wat na verloop van tijd duur kan worden.
HVOF-coatings hebben een relatief lange levensduur in gecontroleerde omgevingen, maar zijn gevoelig voor barsten wanneer ze worden blootgesteld aan plotselinge schokken of thermische schommelingen. Regelmatige inspectie en reparatie zijn nodig om consistente prestaties te garanderen, aangezien schade door barsten of delaminatie de beschermende kwaliteiten van de coating aantast.
Wat is plasmaspuiten?
Plasmaspuiten is een thermisch spuitproces waarbij een plasmastraal van hoge temperatuur wordt gebruikt om materialen te smelten en af te zetten op oppervlakken. Het wordt veel gebruikt voor keramische, metalen en samengestelde coatings in industrieën zoals ruimtevaart, automobielindustrie en energieopwekking. Plasmaspuiten is veelzijdig, maar net als andere thermische spuittechnieken is het gebaseerd op een mechanische verbinding die gevoelig is voor delaminatie onder mechanische spanning of temperatuurschommelingen.
In toepassingen met hoge belasting, zoals turbinebladen of motoronderdelen, kunnen plasma-gespoten coatings na verloop van tijd barsten of afschilferen, vooral als ze worden blootgesteld aan schokken, trillingen of temperatuurschommelingen. De poreuze aard van veel plasma-gespoten coatings beperkt ook hun corrosiebescherming, waardoor regelmatig onderhoud en opnieuw coaten nodig is om hun effectiviteit in agressieve omgevingen te behouden.
Wat is keramische coating?
Keramische coatings staan bekend om hun hoge temperatuurbestendigheid en worden vaak toegepast in luchtvaart- en auto-onderdelen, zoals uitlaatsystemen en turbines. Deze coatings zijn bestand tegen extreme hitte en dienen als thermische barrières die onderdelen zoals motoronderdelen en uitlaatsystemen beschermen. Keramische coatings zijn echter minder effectief onder mechanische spanning en schokbestendigheid, waardoor ze kwetsbaar zijn voor barsten en afschilferen wanneer ze worden blootgesteld aan fysieke slijtage of trillingen.
In toepassingen waar componenten worden blootgesteld aan zowel hoge temperaturen als fysieke belasting, kunnen keramische coatings bros worden, waardoor ze gevoelig worden voor barsten en afschilferen. Hun inherent poreuze structuur, vooral in zwarte coatings, vergroot hun gevoeligheid voor breuken nog verder. De mechanische hechting van keramische lagen aan het substraat maakt ze kwetsbaar voor delaminatie bij impact of trillingen. In omgevingen met een hoge belasting stelt deze kwetsbaarheid het basismateriaal vaak bloot aan slijtage en corrosie, waardoor het vaak opnieuw moet worden aangebracht of gerepareerd om de bescherming te behouden. In sectoren als de mijnbouw of de productie van zware apparatuur kunnen keramische coatings onvoldoende duurzaam zijn onder abrasieve omstandigheden.
Wat is een plasma transferboog?
Plasma Transfer Arc (PTA) is een geavanceerde techniek voor oppervlakteverbetering die wordt gebruikt om duurzame, slijtvaste coatings aan te brengen op metalen oppervlakken. Met behulp van een hoogenergetische plasmaboog smelt het PTA-proces een metaalpoeder of -draad, waardoor een metallurgische verbinding met het substraat ontstaat voor een robuuste, duurzame laag. PTA-coatings staan bekend om hun sterkte en duurzaamheid en zijn bijzonder geschikt voor toepassingen in veeleisende industrieën zoals olie en gas, mijnbouw en zware machines,
waar onderdelen worden blootgesteld aan extreme slijtage en uitzonderlijke bescherming nodig hebben. Hoewel PTA een veerkrachtige coating oplevert, kan de hogere warmte-inbreng leiden tot een bredere warmte-beïnvloede zone, die mogelijk thermische spanning of vervorming veroorzaakt in dunnere materialen. Daarnaast is PTA meestal meer geschikt voor het creëren van dikkere lagen, wat kan leiden tot meer materiaalgebruik en minder precisie bij het aanbrengen van fijne of uniforme coatings.
Traditionele oppervlaktebehandelingen vs lasercladding
In tegenstelling tot traditionele methoden zorgt lasercladding voor een metallurgische verbinding voor een sterkere hechting en biedt het superieure slijtvastheid en corrosiebescherming zonder de poreusheidsproblemen die optreden bij NiCr en HVOF. Hoewel de initiële kosten hoger kunnen zijn, resulteert lasercladden in aanzienlijke besparingen op de lange termijn doordat er minder vaak reparaties en vervangingen nodig zijn. Lasercladding wordt ook steeds geschikter voor een reeks toepassingen naarmate de kosten dalen, waardoor het een uitstekend alternatief is voor traditionele coatings voor zowel zware als lichtere industriële toepassingen.