Traditionelle Methoden der Oberflächenbehandlung
Traditionelle Oberflächenbehandlungen und -beschichtungen sind seit langem der Standard für Industrien, die Korrosionsschutz und Verschleißfestigkeit für kritische Komponenten suchen. Diese Methoden, darunter Hartverchromung, Keramikbeschichtung, Nickelverchromung und thermische Spritztechniken wie das HVOF-Spritzen, werden häufig eingesetzt, um die Lebensdauer von Industrieanlagen zu verlängern. Jede dieser Methoden ist jedoch mit Einschränkungen verbunden, wie z. B. schlechte Haftung, Porosität und Umweltbelastung.
Vorteile des Laserauftragschweißens
Das Laserauftragsschweißen hingegen löst viele dieser Probleme, indem es eine metallurgische Verbindung zwischen dem Grundmaterial und der Beschichtung herstellt. Das Ergebnis ist eine dichtere, porenfreie und äußerst verschleißfeste Schicht, die sich ideal für anspruchsvolle Umgebungen und Anwendungen eignet. Die Kosten des Laserauftragsschweißens sinken ständig, so dass es sich nicht nur für Schwerlastanwendungen, sondern zunehmend auch für leichtere industrielle Anforderungen eignet. Dadurch erhöht das Laserauftragsschweißen nicht nur die Haltbarkeit, sondern verringert auch den Wartungsaufwand und senkt die Gesamtbetriebskosten (TCO) für kritische Komponenten.
Auf dieser Seite geben wir eine kurze Einführung in jede Technik. Weitere Informationen zu den Unterschieden und Vorteilen des Laserstrahl-Auftragschweißens finden Sie auf unserer Vergleichsseite zum Laserstrahl-Auftragschweißen oder kontaktieren Sie uns direkt.
Die gebräuchlichsten traditionellen Methoden können wie folgt kategorisiert werden:
Galvanische Behandlungen
Thermische Sprühverfahren
Andere
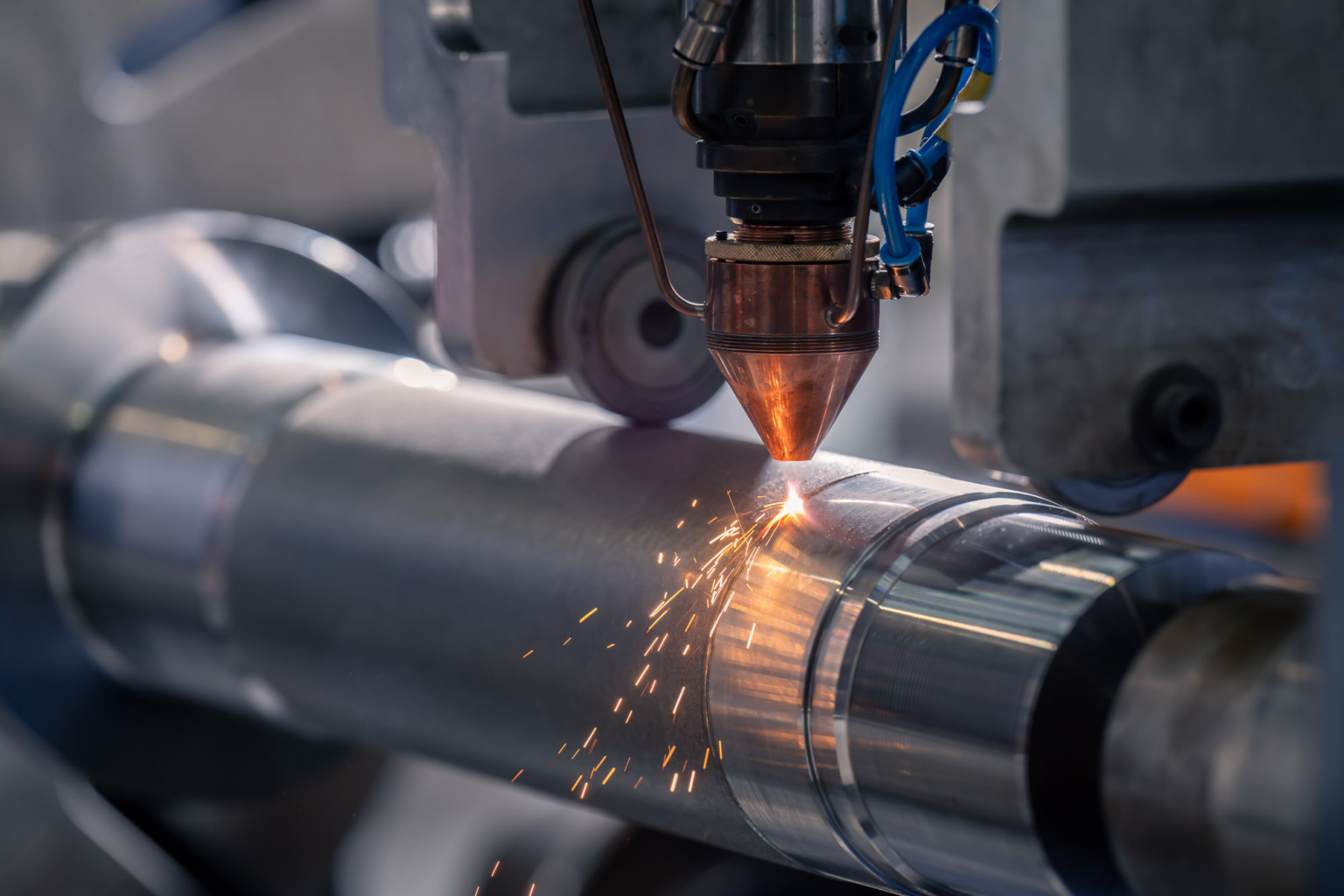
Was ist Hartverchromen?
Bei der Hartverchromung wird eine dünne Chromschicht galvanisch auf Metalloberflächen aufgebracht, um die Verschleiß- und Korrosionsbeständigkeit von Anwendungen wie Hydraulikzylindern und Walzen zu erhöhen. Trotz ihrer weit verbreiteten Verwendung in Branchen wie der verarbeitenden Industrie oder der Offshore-Industrie ist die Hartverchromung jedoch dafür bekannt, dass sie in anspruchsvollen Umgebungen einige entscheidende Schwachstellen aufweist. Die Chromschicht ist mechanisch gebunden, was bei starker Belastung oder Temperaturschwankungen zu schlechter Haftung und Rissbildung führen kann. Obwohl Hartchrom eine widerstandsfähige Außenschicht bildet, ist sie spröde und neigt zum Abblättern oder Abplatzen, wenn sie Stößen oder ständiger mechanischer Belastung ausgesetzt ist, was ihre Haltbarkeit in anspruchsvollen Umgebungen einschränkt.
Hartverchromung ist auch anfällig für Lochfraß und Rostbildung, wenn sie Feuchtigkeit ausgesetzt ist, insbesondere wenn die schützende Ölschicht auf den Zylinderstangen aufgrund mangelnder Bewegung fehlt und die beschichtete Oberfläche den Elementen ausgesetzt ist. Außerdem wird bei diesem Verfahren hexavalentes Chrom (Cr6) verwendet. Chrom-6 ist eine Chemikalie, die häufig in verschiedenen industriellen Beschichtungen verwendet wird, die jedoch mit ernsthaften Gesundheitsrisiken verbunden ist. Aus diesem Grund hat die Europäische Kommission ihre Verwendung erheblich eingeschränkt, und es wird erwartet, dass nach den derzeitigen Vorschriften ein vollständiges Verbot ausgesprochen wird. Während Hartchrom unter moderaten Bedingungen mehrere Jahre halten kann, muss es in aggressiveren Umgebungen häufig gewartet werden, z. B. durch erneutes Auftragen und Polieren, um seine Schutzeigenschaften zu erhalten.
Was ist eine Nickel-Chrom-Beschichtung?
Bei der Nickel-Chrom-Beschichtung wird eine Nickel-Basisschicht mit einer Chrom-Deckschicht kombiniert, um eine glänzende, korrosionsbeständige Oberfläche zu erhalten, die üblicherweise für verschiedene industrielle Komponenten wie Kolbenstangen und Ventile verwendet wird. Obwohl die NiCr-Beschichtung eine mäßige Korrosionsbeständigkeit bietet, ist sie in stark beanspruchten oder korrosiven Umgebungen, wie sie in der Öl- und Gasindustrie, der Schifffahrt und im Schwermaschinenbau anzutreffen sind, nur bedingt einsetzbar.
Unter rauen Bedingungen entstehen in der Nickel-Chrom-Schicht oft Mikrorisse, durch die Feuchtigkeit und Chemikalien in die Oberfläche eindringen und zu Korrosion unter der Beschichtung führen. Besonders problematisch ist dies bei Hydraulik-Zylinderstangen, die lange Zeit im Freien ohne schützenden Ölfilm liegen, was Korrosion und Verschleiß beschleunigen kann. Aufgrund seiner porösen Beschaffenheit bietet NiCr keine vollständig versiegelte Oberfläche, so dass das Grundmaterial im Laufe der Zeit beschädigt werden kann, was kostspielige Reparaturen oder Ersatz erforderlich machen kann.
Was ist Thermisches Spritzen?
Thermisches Spritzen bezieht sich auf eine Reihe von Verfahren, bei denen erhitzte oder geschmolzene Materialien auf eine Oberfläche gesprüht werden, um eine Schutzschicht zu erzeugen. Das thermische Spritzen wird in Branchen wie der Luft- und Raumfahrt und der Energieerzeugung eingesetzt und ermöglicht das Aufbringen von Beschichtungen aus Legierungen, Keramik und Verbundwerkstoffen. Der Hauptvorteil des thermischen Spritzens liegt in seiner Vielseitigkeit, da es große Oberflächen mit relativ dicken Schichten beschichten kann. Allerdings sind thermische Spritzschichten, einschließlich des Plasmaspritzens, in der Regel mechanisch mit dem Substrat verbunden, was bedeutet, dass ihnen die metallurgische Bindung fehlt, die das Laserauftragsschweißen bietet. Dadurch sind sie anfälliger für Risse, Abplatzungen und Delaminierung, insbesondere bei starker mechanischer Belastung oder thermischer Beanspruchung.
Während thermisch gespritzte Beschichtungen unter bestimmten Bedingungen eine ausgezeichnete Beständigkeit aufweisen, ist ihre Wirksamkeit in stark korrosiven Umgebungen, in die Feuchtigkeit und Chemikalien eindringen können, begrenzt, was zu einer möglichen Korrosion des darunter liegenden Materials führen kann. Darüber hinaus können thermisch gespritzte Beschichtungen in Anwendungen, in denen die Bauteile sowohl hohen Temperaturen als auch mechanischer Belastung ausgesetzt sind, schneller als erwartet abgenutzt werden. Häufige Inspektionen sind unerlässlich, um Abnutzung oder Schäden frühzeitig zu erkennen, da beschädigte Beschichtungen neu beschichtet werden müssen, um einen angemessenen Schutz zu gewährleisten.
Was ist HVOF-Spritzen?
HVOF-Spritzen (High-Velocity Oxygen Fuel) ist eine spezielle Art des thermischen Spritzens, die für die Herstellung dichter, harter Beschichtungen bekannt ist, die in Branchen wie Luft- und Raumfahrt, Öl und Gas sowie Schwermaschinenbau weit verbreitet sind. HVOF bietet eine hervorragende Verschleißfestigkeit, insbesondere in abrasiven und korrosiven Umgebungen. Trotz ihrer Härte beruht die HVOF-Beschichtung jedoch auf mechanischer Bindung, was sie anfällig für Delaminierung und Mikrorisse bei starken Stößen oder schwankenden Temperaturen macht. Außerdem ist der Korrosionsschutz durch die poröse Beschaffenheit von HVOF begrenzt, so dass es für aggressive korrosive Umgebungen weniger geeignet ist. Bei Anwendungen wie Hydraulikzylindern und Pumpenwellen kann es erforderlich sein, HVOF regelmäßig neu aufzutragen, um Verschleiß oder Schäden zu beheben, was mit der Zeit teuer werden kann.
HVOF-Beschichtungen haben in kontrollierten Umgebungen eine relativ lange Lebensdauer, sind jedoch anfällig für Risse, wenn sie plötzlichen Stößen oder Temperaturschwankungen ausgesetzt sind. Regelmäßige Inspektionen und Reparaturen sind erforderlich, um eine gleichbleibende Leistung zu gewährleisten, da Schäden durch Risse oder Delaminationen die Schutzwirkung der Beschichtung beeinträchtigen.
Was ist Plasmaspritzen?
Das Plasmaspritzen ist ein thermisches Spritzverfahren, bei dem ein Hochtemperatur-Plasmastrahl verwendet wird, um Materialien zu schmelzen und auf Oberflächen aufzubringen. Es wird häufig für keramische, metallische und Verbundstoffbeschichtungen in Branchen wie der Luft- und Raumfahrt, der Automobilindustrie und der Energieerzeugung eingesetzt. Das Plasmaspritzen ist vielseitig, aber wie andere thermische Spritzverfahren beruht es auf einer mechanischen Verbindung, die bei mechanischer Belastung oder Temperaturschwankungen zur Delamination neigt.
Bei stark beanspruchten Anwendungen wie Turbinenschaufeln oder Motorkomponenten können plasmagespritzte Beschichtungen im Laufe der Zeit reißen oder abblättern, insbesondere wenn sie Stößen, Vibrationen oder Temperaturschwankungen ausgesetzt sind. Die poröse Beschaffenheit vieler plasmagespritzter Beschichtungen schränkt auch ihren Korrosionsschutz ein, so dass eine regelmäßige Wartung und Neubeschichtung erforderlich ist, um ihre Wirksamkeit in aggressiven Umgebungen zu erhalten.
Was ist eine keramische Beschichtung?
Keramische Beschichtungen sind für ihre Hochtemperaturbeständigkeit bekannt und werden häufig in Bauteilen der Luft- und Raumfahrt sowie der Automobilindustrie eingesetzt, z. B. in Abgassystemen und Turbinen. Diese Beschichtungen halten extremer Hitze stand und dienen als thermische Barrieren, die Teile wie Motorteile und Abgassysteme schützen. Allerdings sind keramische Beschichtungen bei mechanischer Beanspruchung und Stoßfestigkeit weniger effektiv, so dass sie bei physischer Abnutzung oder Vibration anfällig für Risse und Abplatzungen sind.
Bei Anwendungen, bei denen Bauteile sowohl hohen Temperaturen als auch physischen Belastungen ausgesetzt sind, können keramische Beschichtungen spröde werden, was sie anfällig für Risse und Abplatzungen macht. Ihre inhärent poröse Struktur, insbesondere bei schwarzen Beschichtungen, erhöht ihre Bruchanfälligkeit zusätzlich. Die mechanische Bindung der keramischen Schichten an das Substrat macht sie anfällig für Delaminationen bei Stößen oder Vibrationen. In hochbelasteten Umgebungen setzt diese Anfälligkeit das Basismaterial häufig dem Verschleiß und der Korrosion aus, so dass eine häufige Neuanbringung oder Reparatur erforderlich ist, um den Schutz aufrechtzuerhalten. In Branchen wie dem Bergbau oder dem Schwermaschinenbau sind keramische Beschichtungen für eine langfristige Haltbarkeit unter abrasiven Bedingungen möglicherweise nicht ausreichend.
Was ist ein Plasma-Transferbogen?
Plasma-Transferbogen (Plasma Transfer Arc, PTA) ist eine fortschrittliche Technik zur Oberflächenveredelung, mit der dauerhafte, verschleißfeste Beschichtungen auf Metalloberflächen aufgebracht werden. Mit Hilfe eines Hochenergie-Plasmalichtbogens schmilzt das PTA-Verfahren ein Metallpulver oder einen Metalldraht und schafft so eine metallurgische Verbindung mit dem Substrat für eine robuste, lang anhaltende Schicht. PTA-Beschichtungen sind für ihre Festigkeit und Haltbarkeit bekannt und eignen sich besonders für Anwendungen in anspruchsvollen Branchen wie Öl und Gas, Bergbau und Schwermaschinenbau,
wo Bauteile extremem Verschleiß ausgesetzt sind und einen außergewöhnlichen Schutz benötigen. Obwohl PTA eine widerstandsfähige Beschichtung bietet, kann die höhere Wärmezufuhr zu einer breiteren Wärmeeinflusszone führen, was bei dünneren Materialien zu thermischer Belastung oder Verformung führen kann. Außerdem eignet sich PTA in der Regel besser für die Herstellung dickerer Schichten, was zu einem höheren Materialverbrauch und weniger Präzision beim Auftragen feiner oder gleichmäßiger Beschichtungen führen kann.
Traditionelle Oberflächenbehandlung vs. Laserstrahlbeschichtung
Im Gegensatz zu herkömmlichen Verfahren sorgt das Laserauftragsschweißen für eine metallurgische Bindung, die eine stärkere Haftung ermöglicht, und bietet eine höhere Verschleißfestigkeit und einen besseren Korrosionsschutz ohne die bei NiCr und HVOF auftretenden Porositätsprobleme. Auch wenn die anfänglichen Kosten höher sind, führt das Laserauftragsschweißen langfristig zu erheblichen Einsparungen, da weniger häufige Reparaturen und Ersatzbeschichtungen erforderlich sind. Da die Kosten sinken, eignet sich das Laserauftragsschweißen zunehmend für eine Reihe von Anwendungen und ist damit eine hervorragende Alternative zu herkömmlichen Beschichtungen sowohl für schwere als auch für leichtere industrielle Anwendungen.