Méthodes traditionnelles de traitement de surface
Les traitements de surface traditionnels et les revêtements de surface ont longtemps été la norme pour les industries cherchant à protéger leurs composants critiques contre la corrosion et l’usure. Ces méthodes, telles que le chromage dur, le revêtement céramique, le placage nickel-chrome et les techniques de projection thermique comme la pulvérisation HVOF, sont largement utilisées pour prolonger la durée de vie des équipements industriels. Cependant, chacune de ces méthodes présente des limitations, notamment une mauvaise adhérence, une porosité et un impact environnemental négatif.
Avantages du rechargement laser
Le rechargement laser ou Laser Cladding, en revanche, résout bon nombre de ces problèmes en créant une liaison métallurgique entre le matériau de base et la couche de revêtement. Cela permet d’obtenir une couche plus dense, non poreuse et hautement résistante à l’usure, ce qui en fait une solution idéale pour des environnements et des applications exigeants. Avec la baisse progressive des coûts, le rechargement laser devient une option de plus en plus accessible, non seulement pour les usages intensifs, mais aussi pour les besoins industriels plus légers. En optant pour cette solution, vous renforcez la durabilité de vos composants critiques tout en réduisant les coûts de maintenance et le coût total de possession (TOC).
Cette page vous propose une présentation concise des principales techniques utilisées dans les traitements de surface. Si vous souhaitez en savoir davantage sur les différences et les avantages du rechargement laser, consultez notre page dédiée à la comparaison des technologies ou contactez-nous directement.
Les méthodes traditionnelles les plus courantes sont regroupées dans les catégories suivantes :
Traitements galvaniques
Méthodes de projection thermique
Autres
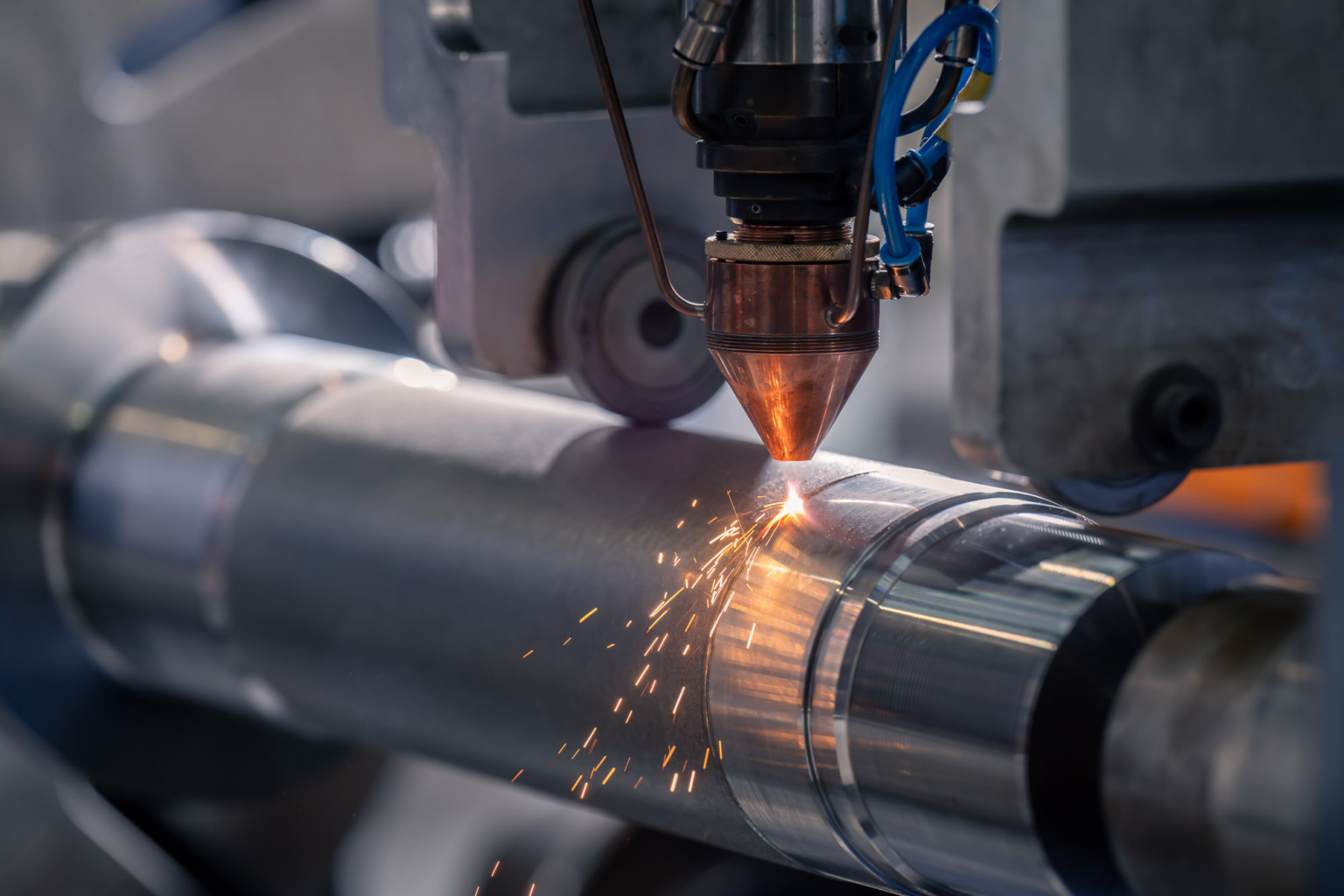
Qu'est-ce que le chromage dur ?
Le chromage dur consiste à appliquer, par électrodéposition, une fine couche de chrome sur des surfaces métalliques afin d’améliorer leur résistance à l’usure et à la corrosion. Ce procédé est couramment utilisé pour des applications telles que les vérins hydrauliques et les rouleaux. Cependant, malgré son utilisation répandue dans des secteurs comme l’industrie manufacturière ou l’offshore, le chromage dur présente plusieurs faiblesses majeures dans les environnements exigeants. La couche de chrome est mécaniquement liée au matériau de base, ce qui peut entraîner une mauvaise adhérence et des fissures sous de lourdes charges ou lors de fluctuations de température. Bien que le chromage dur crée une couche extérieure résistante, celle-ci est fragile et peut se décoller ou s’écailler lorsqu’elle est soumise à des impacts ou à un stress mécanique continu, ce qui limite sa durabilité dans des conditions extrêmes.
Le chromage dur est également vulnérable à la formation de piqûres et de rouille lorsqu’il est exposé à l’humidité, en particulier lorsque la couche protectrice d’huile sur les tiges de vérins est absente à cause d’un manque de mouvement, laissant ainsi la surface exposée aux éléments. De plus, ce procédé implique l’utilisation de chrome hexavalent (Cr6), un produit chimique couramment utilisé dans divers revêtements industriels, mais connu pour ses risques graves pour la santé. En conséquence, la Commission européenne en a considérablement restreint l’utilisation, et une interdiction complète est attendue dans le cadre des réglementations actuelles. Bien que le chromage dur puisse durer plusieurs années dans des conditions modérées, il nécessite souvent un entretien régulier, comme des réapplications et un polissage, pour maintenir ses propriétés protectrices dans des environnements plus agressifs.
Qu’est-ce que le placage nickel-chrome ?
Le placage nickel-chrome combine une couche de base en nickel avec une couche supérieure de chrome pour offrir une finition brillante et résistante à la corrosion. Ce procédé est couramment utilisé pour divers composants industriels tels que les tiges de piston et les soupapes. Bien que le placage NiCr offre une résistance modérée à la corrosion, il montre ses limites dans des environnements soumis à des contraintes élevées ou fortement corrosifs, comme ceux rencontrés dans les industries du pétrole et gaz, du maritime, et des machines lourdes.
Dans des conditions difficiles, des microfissures se développent souvent dans la couche de nickel-chrome, permettant à l’humidité et aux produits chimiques de pénétrer jusqu’à la surface sous-jacente, provoquant ainsi une corrosion sous le revêtement. Ce problème est particulièrement critique pour les tiges de vérins hydrauliques, où une exposition prolongée à des environnements extérieurs, sans film protecteur d’huile, accélère la corrosion et l’usure. En raison de sa nature poreuse, le placage NiCr ne garantit pas une surface entièrement étanche, laissant le matériau de base vulnérable aux dommages au fil du temps, ce qui peut entraîner des réparations ou des remplacements coûteux.
Qu’est-ce que la projection thermique ?
La projection thermique regroupe une famille de procédés consistant à pulvériser des matériaux chauffés ou fondus sur une surface pour créer un revêtement protecteur. Utilisée dans des secteurs tels que l’aérospatiale et la production d’énergie, cette technologie permet d’appliquer des revêtements composés d’alliages, de céramiques et de composites. L’un des principaux avantages de la projection thermique réside dans sa polyvalence : elle peut recouvrir de grandes surfaces avec des couches relativement épaisses. Cependant, les revêtements issus de la projection thermique, comme ceux obtenus par pulvérisation plasma, sont généralement liés mécaniquement au substrat. Contrairement au rechargement laser, ou Laser Cladding, ils ne forment pas de liaison métallurgique, ce qui les rend plus sujets aux fissures, à l’écaillage et à la délamination, en particulier sous de fortes charges mécaniques ou lors de cycles thermiques.
Bien que ces revêtements puissent offrir une bonne résistance dans certaines conditions, leur porosité limite leur efficacité dans des environnements très corrosifs. L’humidité et les produits chimiques peuvent s’infiltrer, provoquant ainsi la corrosion du matériau sous-jacent. De plus, dans des applications où les composants sont exposés à des températures élevées et à des contraintes mécaniques, les revêtements thermiques peuvent se détériorer plus rapidement que prévu. Des inspections fréquentes sont nécessaires pour détecter toute usure ou dommage, car les revêtements abîmés doivent être réappliqués pour garantir une protection adéquate.
Qu’est-ce que la pulvérisation HVOF ?
La pulvérisation HVOF (High-Velocity Oxygen Fuel) est une technique spécifique de projection thermique réputée pour produire des revêtements denses et résistants. Ces revêtements sont largement utilisés dans des industries telles que l’aérospatiale, le pétrole et gaz, ainsi que la machinerie lourde. La technologie HVOF offre une excellente résistance à l’usure, notamment dans des environnements abrasifs et corrosifs. Cependant, malgré sa dureté, le revêtement HVOF repose sur une liaison mécanique, ce qui le rend vulnérable à la délamination et aux microfissures en cas d’impacts importants ou de fluctuations de température. De plus, la porosité inhérente des revêtements HVOF limite leur protection contre la corrosion, les rendant moins adaptés aux environnements agressivement corrosifs. Par exemple, dans des applications comme les tiges de vérins hydrauliques ou les arbres de pompes, les revêtements HVOF nécessitent souvent des réapplications périodiques pour remédier à l’usure ou aux dommages, ce qui peut engendrer des coûts élevés à long terme.
Bien que les revêtements HVOF aient une durée de vie relativement longue dans des environnements contrôlés, ils sont sensibles aux fissures lorsqu’ils sont exposés à des impacts soudains ou à des cycles thermiques. Des inspections et des réparations régulières sont nécessaires pour garantir des performances constantes, car des fissures ou une délamination compromettent les propriétés protectrices du revêtement.
Qu’est-ce que la pulvérisation plasma ?
La pulvérisation plasma est un procédé de projection thermique utilisant un jet de plasma à haute température pour fondre et déposer des matériaux sur des surfaces. Cette technique est largement utilisée pour appliquer des revêtements en céramique, en métal ou en composite dans des secteurs comme l’aérospatiale, l’automobile et la production d’énergie. Bien qu’elle soit très polyvalente, la pulvérisation plasma, comme d’autres techniques de projection thermique, repose sur une liaison mécanique. Cela la rend sujette à la délamination en cas de contraintes mécaniques ou de cycles thermiques.
Dans des applications exigeantes, telles que les pales de turbines ou les composants de moteur, les revêtements obtenus par pulvérisation plasma peuvent se fissurer ou s’écailler avec le temps, en particulier lorsqu’ils sont soumis à des impacts, des vibrations ou des fluctuations de température. De plus, la porosité de nombreux revêtements plasma limite leur capacité à protéger efficacement contre la corrosion, rendant nécessaire un entretien régulier et des réapplications pour garantir leur efficacité dans des environnements agressifs.
Qu’est-ce qu’un revêtement céramique ?
Les revêtements céramiques sont réputés pour leur résistance aux hautes températures et sont souvent utilisés sur des composants aérospatiaux et automobiles, tels que les systèmes d’échappement et les turbines. Ces revêtements agissent comme des barrières thermiques, protégeant les pièces des températures extrêmes, par exemple dans les moteurs ou les systèmes d’échappement. Cependant, les revêtements céramiques sont moins performants face aux contraintes mécaniques et aux impacts. Ils sont ainsi vulnérables aux fissures et à l’écaillage lorsqu’ils sont soumis à une usure physique ou à des vibrations.
Dans des applications où les composants sont exposés à la fois à des températures élevées et à des contraintes physiques, ces revêtements peuvent devenir cassants, augmentant leur sensibilité aux fissures et aux dommages. La structure naturellement poreuse des revêtements céramiques, notamment ceux de couleur noire, accentue leur fragilité et leur propension aux fractures. De plus, la liaison mécanique des couches céramiques au substrat les rend vulnérables à la délamination en cas d’impacts ou de vibrations. Dans des environnements à fortes charges, cette faiblesse expose souvent le matériau de base à l’usure et à la corrosion, nécessitant des réparations ou des réapplications fréquentes pour maintenir la protection. Dans des secteurs comme l’exploitation minière ou la fabrication d’équipements lourds, les revêtements céramiques peuvent s’avérer insuffisants pour garantir une durabilité à long terme dans des conditions abrasives.
Qu’est-ce que l’arc plasma transféré (PTA) ?
L’arc plasma transféré (Plasma Transfer Arc, PTA) est une technique avancée d’amélioration des surfaces utilisée pour appliquer des revêtements durables et résistants à l’usure sur des surfaces métalliques. En utilisant un arc plasma à haute énergie, le procédé PTA fait fondre une poudre ou un fil métallique, créant ainsi une liaison métallurgique avec le substrat. Le résultat est une couche robuste et durable. Reconnu pour sa résistance et sa durabilité, le revêtement PTA est particulièrement adapté aux secteurs exigeants tels que le pétrole et le gaz, l’exploitation minière, et la machinerie lourde.
Ces environnements exposent les composants à une usure extrême, nécessitant une protection exceptionnelle. Cependant, bien que le PTA fournisse un revêtement résistant, la chaleur élevée générée par le procédé peut entraîner une zone thermiquement affectée plus large, susceptible de provoquer des contraintes thermiques ou des distorsions sur les matériaux plus fins. De plus, le PTA est généralement mieux adapté à la création de couches épaisses, ce qui peut augmenter la consommation de matériau et réduire la précision pour des revêtements fins ou uniformes.
Traitements de surface traditionnels vs rechargement laser
Contrairement aux méthodes traditionnelles, le rechargement laser offre une liaison métallurgique qui garantit une adhérence plus solide et une résistance supérieure à l’usure et à la corrosion. Il élimine également les problèmes de porosité observés dans les revêtements NiCr et HVOF. Bien que les coûts initiaux soient parfois plus élevés, le rechargement laser génère des économies significatives à long terme en réduisant le besoin de réparations et de remplacements fréquents. Avec la baisse progressive des coûts, le rechargement laser devient une alternative idéale aux revêtements traditionnels, que ce soit pour des applications intensives ou des besoins industriels plus légers.